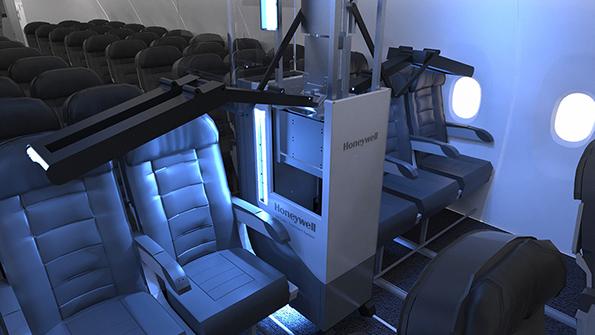
Just as the 9/11 terrorist attacks in 2001 led to worldwide changes in air transport security, COVID-19 has accelerated the development and introduction of new sanitary, contactless and health care systems for air travel.
Thermal scanners, antibacterial coatings, ultraviolet lights and mobile technology systems and processes are being tailored to airline and airport use in a bid to instill passenger and employee confidence that it safe to fly.
Already, the focus on which technologies to use has changed. During the early onset of the virus, some airports rolled out thermal screening stations across gateways because it was assumed infected people exhibited symptoms, such as fever. The sensors ranged from large thermal rigs to manual infrared thermometers.
But hand-held thermometers can place employees at risk, while the rigs have a poor accuracy rate, Rik Heller, founder and CEO of Wello, points out. And not all infected people exhibit fever or any other symptoms.
Wello has deployed the welloStationX automated contactless temperature screening station at Dallas Love Field Airport in Texas. This system records an individual’s temperature and photo and prints an “all clear” ID tag if the temperature is normal. If an elevated temperature is detected, an alert is sent via text or email to a facility representative. It is currently the only such scanner approved by the US Food and Drug Administration for this purpose.
Heller says the company is also piloting some programs using artificial intelligence to determine what is normal and what is an elevated temperature for an individual, because normal temperatures can vary depending on a person’s age and sex. Flu studies have shown that people with normal body temperatures are less contagious than those with mild fevers, who in turn are less contagious than those with high fevers, so agencies are also looking at the “contagiousness” factor.
“The best technology isn’t the sharpest sensor, it’s the one that understands what is normal temperature and is accurate enough to identify even slightly elevated temperatures,” Heller said.

Coat it
Along with thermal scanners, antibacterial coatings suddenly became in demand to disinfect high-touch areas. Common noncorrosive and nonflammable coatings use silver or titanium dioxide and last up to just 90 days.
Singapore Technologies (ST) Engineering, together with another Singapore company, developed the world’s first antimicrobial with fusion resonance technology, known as the Plasma ResoShield. The water-based coating creates a plasma shield that eliminates pathogens before they reach the surface, providing a full year of protection.
But the industry has yet to create standards for which types of antibacterial products are recommended for aircraft use.
“Having an international standard will help the companies to develop the right products for the right use and save the transaction costs,” ST Engineering VP-commercial business at the company’s engineering & development center Tan Hean Seng said.
“Currently, there are different standards by authorities from different countries. It will be difficult and costly without clear standard guidelines. An international standard or guideline would definitely help the end users in saving their time spent on research,” he said.
Tan believes that future interiors will see antibacterial technology being incorporated into raw aircraft materials like textile fibers, composite panels and laminates and being built into the finished product. He says coatings and contactless technologies work hand in hand, since there are areas like armrests where touchless technology cannot replace an antibacterial coating to protect passengers.
Avoid It
Before the coronavirus outbreak, airlines and airports were already working on some digitalization and contactless initiatives aimed at speeding up the check-in and boarding processes. These included introducing mobile applications that support digital boarding passes and the rolling out of biometric systems that utilize facial and iris recognition. Post-outbreak, suppliers have seen an increased interest in these technologies, many of which are being accelerated to complement less sophisticated measures, like social distancing and mask wearing.
SITA Asia-Pacific president Sumesh Patel sees biometric systems and mobile applications providing the way forward for contactless technology. The tech company is developing a series of mobile applications that will enable mobile phones to be used as remote controls for check-in kiosks simply by scanning a quick response (QR) code on the kiosk screen. There are also studies aiming to integrate travel declaration forms and COVID-19 test results into an Advanced Passenger Processing system, allowing receiving immigration agencies to access the data in advance.
Patel said some airports are making the long-term investments in biometric systems, while those wary of capital expenditures are looking at the SITA SmartFlex solution to supplement their current infrastructure with mobile technology. Beijing Capital Airport (PEK) has recently rolled out an extensive biometric system that enables a touchless end-to-end journey, including duty-free shopping.
Companies like SITA and IBM are also developing mobile applications to facilitate physical distancing in areas susceptible to crowding, such as boarding gates and baggage carousels. For example, IBM’s Virtual Gate informs passengers of their upgrade or standby status without the need to check with a gate agent. Passengers can also be informed when it is their turn to go to the gate and board.
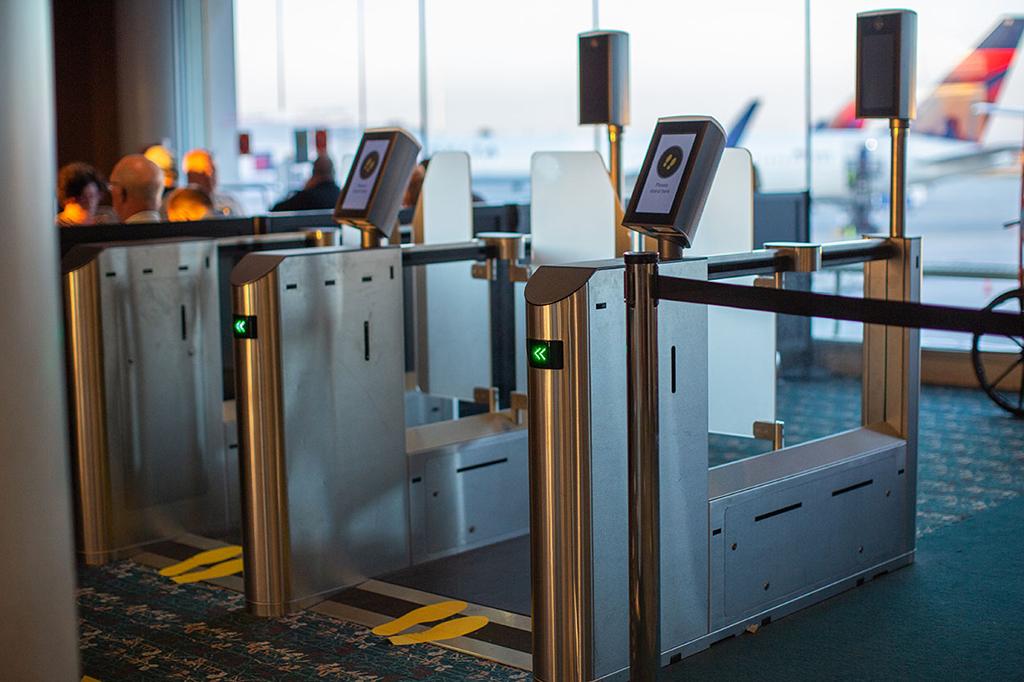
Zap It
To address the growing need to sanitize touchpoints on aircraft, aerospace suppliers are looking for new partnerships with companies outside the aviation industry.
Honeywell, in partnership with Dimer, was one of the first aerospace suppliers to introduce ultraviolet-C (UVC) lights for aviation application in the form of the UV Cabin System. UVC operates on the 253.7 nm wavelength, commonly known as germicidal UV light, and is clinically proven to kill bacteria and viruses at rates as high as 90% to 99.9% depending on the dosage.
The UV Cabin System features two extendable arms, delivering UVC light on interior surfaces, and a single operator can cover the interior of an Airbus A320 or Boeing 737 in five to eight minutes. JetBlue Airways, Azul Airlines and Qatar Airways are now testing or using the system.
While studies show a slight change in appearance on most cabin materials after being exposed to high UV dosages, it would take around 10 years of constant application for that to occur.
Boeing has partnered with Florida-based Healthe to develop and manufacture a hand-held UV wand that operates on the 222 nm far-UV wavelength, which is reportedly safer for prolonged human contact.
In general, the aviation industry is calling for greater collaboration on these types of initiatives.
“This is a challenging time where the industry must work hand-in-hand,” Honeywell Aerospace VP Brian Wenig said.
“The change in the current travel landscape requires visible technologies and protective measures to regain the traveler’s trust and save airlines. I am not surprised to see even more collaborations within the industry or between different industries, leveraging the different expertise and technologies to create solutions that can help the travel industry navigate through these unprecedented times.”
Heller agrees. “In order to move forward and beat this pandemic, we must collaborate. This includes coordinated research and development, creating joint response plans and executing them,” he said. “To do this we must facilitate a joint sense of ownership and a joint mission to beat the virus and continue to travel without fear.”