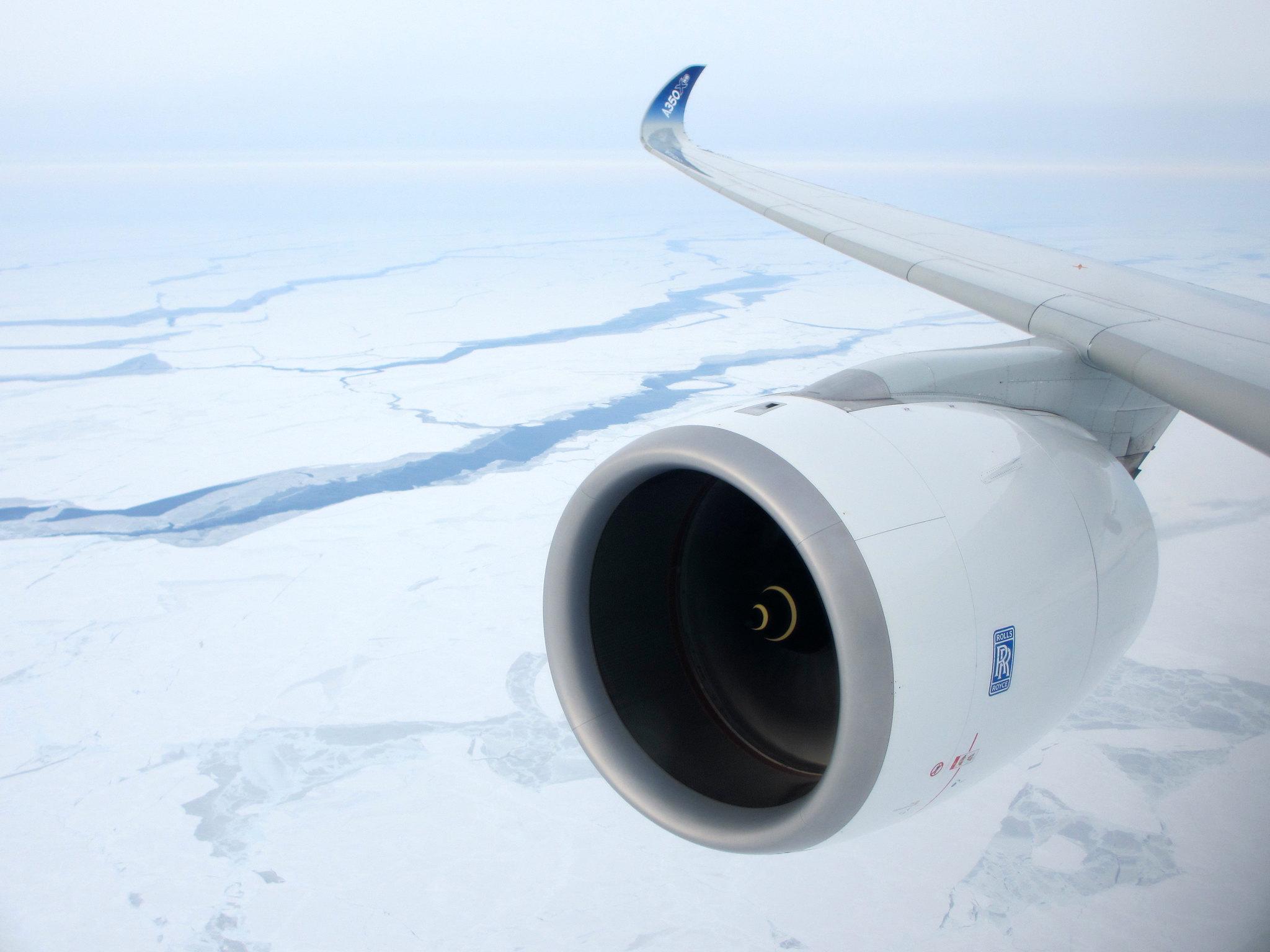
Rolls-Royce has discovered cracks in the intermediate pressure (IP) compressor blades of higher-time Trent XWB-84 engines during scheduled overhaul but said early detection will enable the speedy development of a fix.
The issue does not threaten the long-term reliability of the engine built to power the Airbus A350-900, Rolls said.
The cracks were found in the roots of a limited population of first-stage IP compressor blades of engines undergoing their first overhaul since entering service on the A350 in 2015 and 2016.
However, unlike the well-documented wear and corrosion issues experienced on the Boeing 787’s Trent 1000, the XWB problem “is much more benign, and we have found it before it found us,” Rolls chief engineer for large engines Frank Haselbach said.
Rolls-Royce announced earlier this year an exceptional charge of $1.77 billion (£1.50 billion) related to the ongoing fixes for the Trent 1000, and is moving proactively to reassure A350 operators that the wear issue discovered on the XWB is insignificant by comparison.
The engine-maker, which expects EASA to make the IP compressor inspections the subject of an imminent airworthiness directive, meanwhile remains in the middle of cost-cutting efforts to combat losses associated with the impact of the COVID-19 pandemic.
Describing the cracks as “clear wear and tear in the actual bedding area of the first stage rotor blade,” Haselbach added “we didn’t expect that to happen on the XWB.” Similar issues occurred on the first and second rotor stages of the Trent 1000 IP compressor, and were later traced to resonance caused by wake interactions with upstream stages. However, when Rolls first checked the XWB-84 fleet for similar issues as it tackled the Trent 1000 crack problem, it found none.
Underlining the late service life onset of the condition, Haselbach said “nothing has actually happened with any of these engines. There has been no abnormal operation, no vibration, no inflight shutdowns. It’s a case of ‘we have a problem and we need to find out where it’s coming from’. Now we have found it, we’ll have to make sure that we are effectively doing the right thing and scanning the fleet in the appropriate age and actually go to a repeat inspection regime.”
Cracks were found in isolated blades in 20% of the approximately 100 higher time engines inspected to-date. Rolls has so far built around 800 Trent XWB-84s and accumulated six million hours of flight time in what the manufacturer calls the “smoothest entry-into-service of any widebody engine we have developed.”
The vibratory issue will not occur on the more powerful XWB-97 variant used in the A350-1000 because the first two-stages of the IP compressor in this engine are comprised of solid blisks (integrated blades and disks), rather than the XWB-84’s more conventional blade and disk configuration.
The issue on the Airbus engine was unexpected because “fundamentally the aerodynamic forcing of the IP compressor in the XWB is much weaker than on the Trent 1000,” Haselbach said. “We’ll have to see what the investigation gives us but clearly this is something which we’re driving with a lot of speed.”
The trouble-shooting team aims to complete a vibration survey and root-cause analysis by year’s end. In the meantime, affected engines will be retrofitted with new first-stage blades pending the longer-term development of a permanent fix.
Compared to the height of the Trent 1000 crisis in 2018-2019, when Rolls was hamstrung by limited repair and overhaul capacity, the pandemic has changed the picture for the XWB recovery plan. “We actually have more capacity around us than we thought we’d have because of less flying activity and stretched overhaul schedules. So, we have parts and we have the capacity to do it,” Haselbach said.