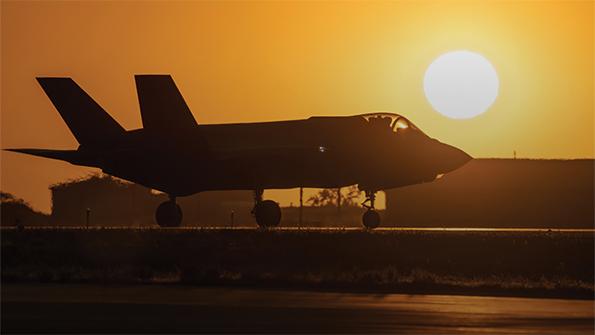
Planned F-35 electronics upgrades will put further pressure on an already overtaxed thermal management system.
A difficult decision looms for the leadership of the Lockheed Martin F-35 program. A major upgrade of the stealth jet’s overloaded cooling system is coming, but should program officials scope the improved thermal management system to address future needs, or should they scope it merely to solve the immediate overheating issues?
The answer could make the difference between a relatively straightforward upgrade and a far more intrusive modification, according to Honeywell Defense and Space, the supplier of the existing power and thermal management system (PTMS) for the F-35.
- Upgrades may address different waste heat levels
- Block 4 upgrade program will worsen cooling shortfall
Matt Milas, president of Honeywell Defense and Space, says he is concerned that program officials are favoring the more radical upgrade option, which he warns would require replacing the cooling system’s “plumbing”—the network of tubes bearing a liquid coolant that snakes through the F-35’s interior, including through the jet’s load-carrying bulkheads.
“That presents a lot of problems because now you have to swap out some of the plumbing,” Milas tells Aviation Week. “When you swap out the plumbing, you have to take the skins off the wings and things like that.”
The F-35 Joint Program Office (JPO) held a PTMS Industry Day on June 12-14 to receive industry feedback on proposals to upgrade the jet’s overwhelmed cooling system. A final decision may still be weeks or months away.
“We are very early into the Defense Acquisition System/Process,” a JPO spokesman told Aviation Week in an email. “All PTMS options will be assessed to ensure we provide the greatest capability to the warfighter.”
The need for a major cooling system upgrade has been a long time coming.
Honeywell’s PTMS siphons hot air from the compressor module of the Pratt & Whitney F135 engine, and that air is dissipated through a fan duct heat exchanger. It is then further dissipated over tubes of polyalphaolefin (PAO) coolant, a fluid that channels the absorbed heat to a PAO-to-air heat exchanger. The air is then cooled further through a recuperator and a loads heat exchanger. Finally, this chilled air is passed through a closed-loop cycle around the F-35’s electronics.
F-35 designers assumed the electronics would need to handle no more than 14 kW of waste heat. That assumption drove the design of key details of the PTMS, including the power output of the motor for the cooling system and the diameter of the tubes feeding the cooling fluid to the PAO-to-air heat exchanger.
Fifteen years ago, however, Lockheed discovered that the cooling system was insufficient, according to a report in May by the Government Accountability Office. Instead of requiring 14 kW of cooling capacity, the Block 3F F-35 demanded up to 32 kW. To close this gap, Lockheed, Pratt and Honeywell adapted the PTMS to siphon twice the amount of air out of the engine as intended, but that has reduced the propulsion system’s longevity and increased repair costs.
The cooling shortfall is widening as the Block 4 upgrade program adds more powerful electronics and sensors. The improvements have increased the requirement for the cooling system to handle up to 47 kW of waste heat. Furthermore, classified upgrades envisioned for the 2030s could drive the requirement up to at least 62 kW—and perhaps as high as 80 kW.
According to Milas, adapting the cooling system capacity to address the needs of the Block 4 requirement is straightforward. “What we could do to get up to the 47 kW is put on a more powerful motor and some more sturdy valves and push the PAO fluid through a little bit faster,” he says.
Jumping to a 62-kW capacity system, however, will require more extensive changes, he notes. “If you want to jump to 62 kW of cooling, you’re not able to do it with the current [diameter] of plumbing,” Milas says. “You’ve only got a certain diameter [of tube], so if you want more heat dissipation off of those, you need more fluid to carry the heat and to take it to the heat exchangers.”
The PAO tubes pass through the F-35’s drilled holes in the internal bulkheads and frames. If the diameter of the tubes increases, the holes in each of the bulkheads and frames also would have to be enlarged, Milas says. “We start making the holes bigger—a quarter-inch—but it adds up and makes a big difference from a structural loads [issue],” he added.
Comments