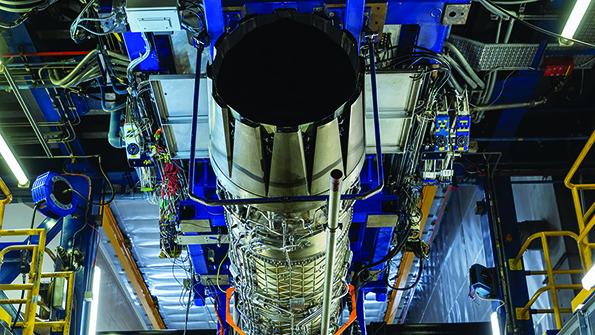
Rolls-Royce EJ200 and 10-m-long engine duct.
Just days before the Paris Air Show, UK industry signaled a lead over its continental counterpart in the development of a flying demonstrator that will de-risk technologies for the Tempest future combat aircraft.
Nearly a year after development of the crewed, supersonic, low-observable aircraft was announced at last year’s Farnborough Airshow, engineers are pressing ahead with a critical design review prior to the anticipated beginning of assembly in 2024-25 and planned first flight in 2027. Meeting these milestones will put the Tempest demonstrator at least two years ahead of the European Future Combat Air System Next-Generation Fighter counterpart now expected to fly in 2029 (AW&ST July 25-Aug. 7, 2022, p. 18).
- Eurofighter’s EJ200 engine will power the demonstrator
- Royal Air Force and BAE test pilots have flown 125 simulated sorties
As part of the demonstrator development effort, the Team Tempest industry participants, including BAE Systems and Rolls-Royce, have developed hybrid ground-test rigs on which to evaluate flight control actuators in conjunction with the flight control system. The team has qualified the demonstrator’s pilot escape system with rocket-sled trials of a Martin-Baker Mk. 16 ejection seat and has completed aerodynamic engine trials, developing a serpentine duct and air intake. This will allow the aircraft’s two Eurojet EJ200 engines, donated by the UK Defense Ministry, to operate across the demonstrator’s full flight envelope.
Development of the demonstrator, for now solely a UK effort, presents an opportunity to “re-brigade” the UK’s combat aircraft enterprise, Neil Strang, Tempest delivery director at BAE, said June 13 at company media briefings here.
“We must use the flying demonstrator as a key opportunity to bring industry to make sure we can redevelop and grow muscle mass and movement and build confidence in the future,” he said.
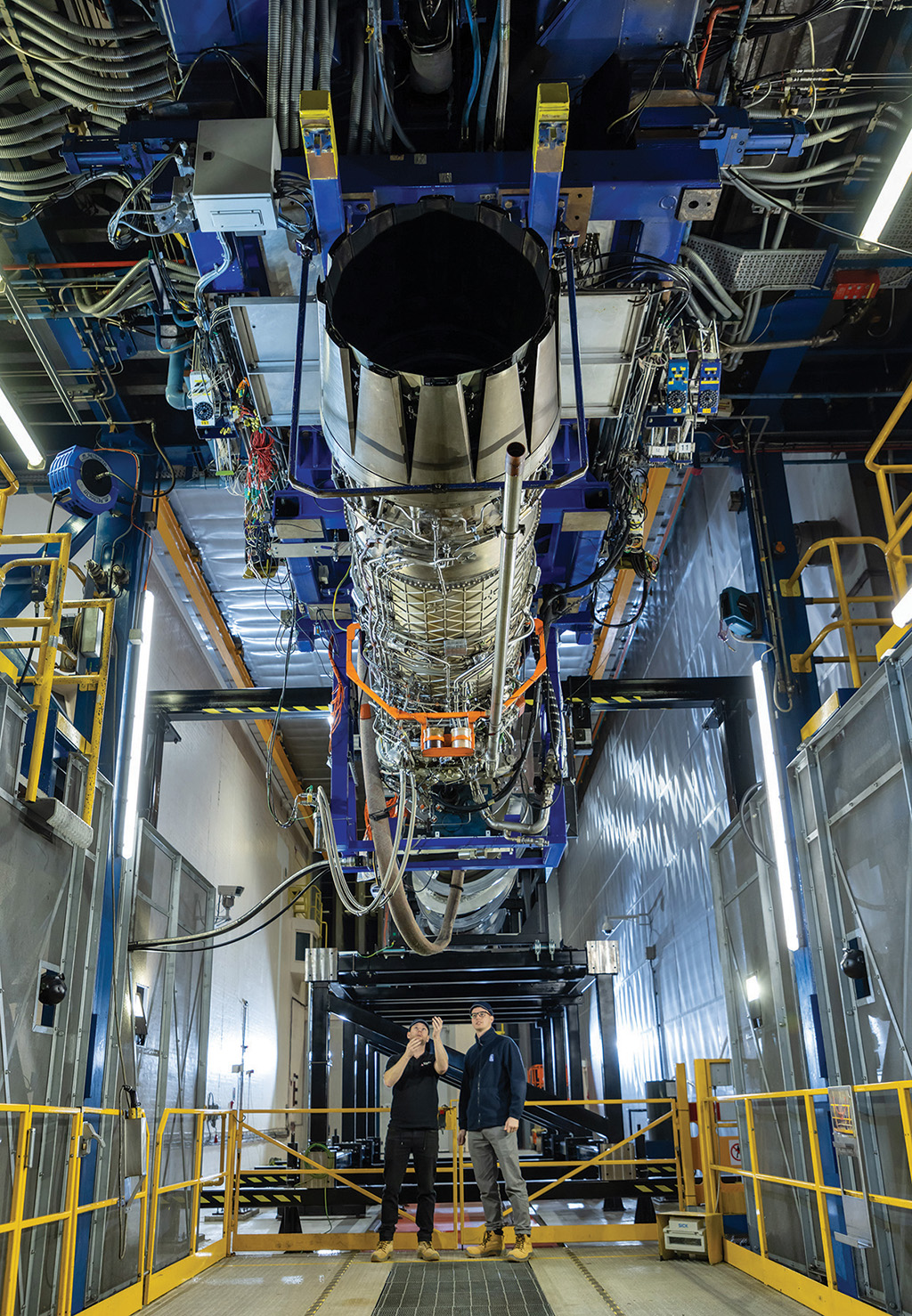
The flying demonstrator is one of three demo programs being developed as part of work on the Tempest combat aircraft and the wider Global Combat Air Program (GCAP) with Italy and Japan. Other major demonstrator programs within the GCAP include the Excalibur Boeing 757 Flight Test Aircraft and the Rolls and IHI Corp. development of a power system—including the combined engine and electrical generation system—that Italy’s Avio Aero recently joined.
The three technology initiatives disclosed by industry on June 13 also hint at the configuration and size of the aircraft.
The engine ducts developed for the demonstrator measure around 10 m (33 ft.) in length, while the engine itself is another 4 m long. Combined, they are almost as long as the 16-m Eurofighter Typhoon.
BAE and Rolls have developed an F-35-like diverterless supersonic inlet for the demonstrator, while the duct itself conditions the flow of air and “makes the EJ200 think that’s its sitting in a Typhoon,” says Conrad Banks, Rolls’ chief engineer for future defense programs. “The challenge [for] BAE is to make sure the quality of air doesn’t go beyond cleared EJ200 limits . . . because if this produces anything outside the existing cleared evidence for the EJ200, we have a real challenge if we can’t use the established flight clearance protocol.”
Ground trials of the engine and duct, performed in Bristol, England, between November 2022 and February 2023, tested the engine while in reheat and with so-called throttle slams and re-slams, where the pilot advances engine power rapidly. This research also has allowed Rolls to validate a toolset that will be essential in the development of the Tempest fighter’s intake and distortion-tolerant fan. They will be a feature of the next-generation GCAP engine under development.
As with other aircraft development programs, BAE is using ground-test rigs to evaluate elements of the aircraft, but it has adopted a hybrid approach that allows these rigs to be linked rather than operated in a siloed manner. This enables the flight control software and open-architecture system to be linked to real hardware and components such as the planned triplex flight control system and Collins Aerospace-supplied flight control actuators. The trials underway are testing four such actuators for three sets of flaperons and a ruddervator vertical stabilizer.
This hybrid approach enables engineers to maximize the use of the rigs. A process called autocoding is turning flight model data into safety-critical system software, and the demonstrator is expected to make use of the UK government-funded Pyramid reusable and open-mission system architecture as well.
In the cockpit, the demonstrator will be flown with a sidestick rather than a central control column as on the Eurofighter, providing additional space for a wide-area cockpit display.
Industry and the UK government have not disclosed how they will use the demonstrator, but Strang says the flight trials will “get after big risks” left over from technology development.