
AeroTEC will perform electric aircraft modifications for Surf Air and MagniX from this narrowbody hangar in Moses Lake.
The pace of hydrogen- and electric-powered aircraft development is accelerating as the technology gains traction. The aviation industry has seen increasing orders this year for these greener aircraft as developers reach major milestones, such as MagniX’s induction of a De Havilland Canada Dash 7 for hybrid-electric modifications and initial flight tests for Universal Hydrogen’s Dash 8-300 hydrogen-electric demonstrator.
Although electric and hydrogen aircraft startups have received most of the industry buzz amid these efforts, engineering services provider AeroTEC has been a quiet driving force behind much of the development, modification, testing and certification work for these next-gen projects.
AeroTEC CEO Lee Human jokingly describes his company’s flight-test center in Moses Lake, Washington, as the “island of misfit aircraft.” Since it was founded in 2003, the company has focused on supplemental type certificate (STC) development, special mission modifications and aftermarket support of the “one-off” aircraft that many major MRO providers might not have the capability or willingness to accommodate.
The company cut its teeth on projects such as the Aviation Partners blended winglet, Mitsubishi Regional Jet and Boeing 737-800 converted freighter, and in more recent years it has expanded into supporting modifications for firefighting aircraft, flying testbeds, and hybrid and electric propulsion conversions. It worked with MagniX in the depth of the pandemic on an all-electric Cessna Caravan and with Eviation on its all-electric Alice aircraft. AeroTEC is now working on several high-profile electric and hydrogen aircraft projects, including MagniX and NASA’s electric propulsion flight demonstrator (EPFD), Surf Air Mobility’s electric Caravan and Universal Hydrogen’s Dash 8 hydrogen technology demonstrator.
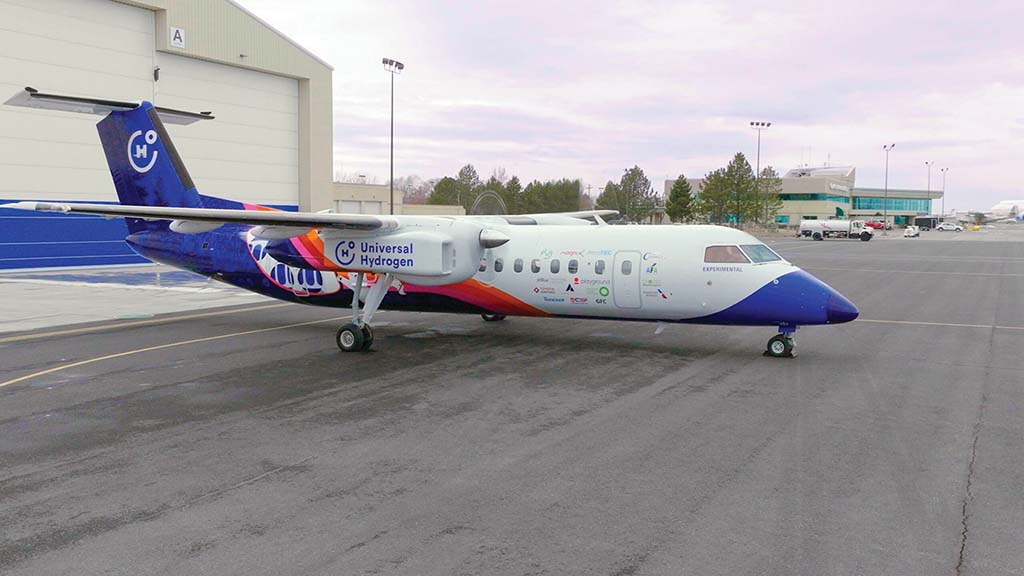
manufacturing, modification and analysis of Universal Hydrogen’s Dash 8 aircraft. Credit: Universal Hydrogen
Of these, Universal Hydrogen’s Dash 8 is one of the furthest along, in the midst of a flight-test campaign. AeroTEC helped Universal Hydrogen with aircraft integration of its hydrogen propulsion system, including conceptual and detail design, parts manufacturing, hands-on aircraft modification, and safety and detail analysis. “When it comes to the wing structure, nacelle and landing gear structure, we reverse-engineered the aircraft to allow us to create our digital mockup to make those modifications and do that design and analysis,” Human explains.
Universal Hydrogen provided the hydrogen tank system, fuel cells and propulsion control system while MagniX provided the electric propulsion unit. Meanwhile, AeroTEC leveraged its manufacturing center in Arlington, Washington, to produce additional parts for the aircraft such as wire harnesses. AeroTEC’s mechanical and technical teams in Moses Lake performed the installation, ground checks and support for test flights.
AeroTEC has finished preliminary design review of the MagniX/NASA EPFD and expects the aircraft, provided by Air Tindi, to arrive soon. Then it will begin baseline flight tests to gather data to validate models and begin modifying the aircraft. Meanwhile, AeroTEC is mapping out the Surf Air eCaravan project and determining suppliers to provide parts and pieces for the aircraft.
Sustainment
Human says AeroTEC intends to be involved in the long-term sustainment of these specialized aircraft. “The first candidate for that will be the Surf Air eCaravan. We’re working toward certification of the world’s first retrofit Cessna Caravan STC, so it will be fully FAA certified,” he says. “We envision being the initial modification center here for the initial entry into service and also the maintenance center, but we have to be realistic. This is going to be a global product, so we need to train and qualify other sites.”
He adds that AeroTEC plans to partner with other MROs to provide training on dealing with high-voltage electronics, batteries and other unique aspects of new-technology aircraft such as the eCaravan. “It’ll probably be five years before there is a meaningful population of new-technology aircraft that will require specialized training and procedures, and we have that advantage, so we’ll definitely lead that market,” he says. “Once the dominos start to fall, we’ll see many new-technology aircraft, and the world will have to catch up pretty quickly.”
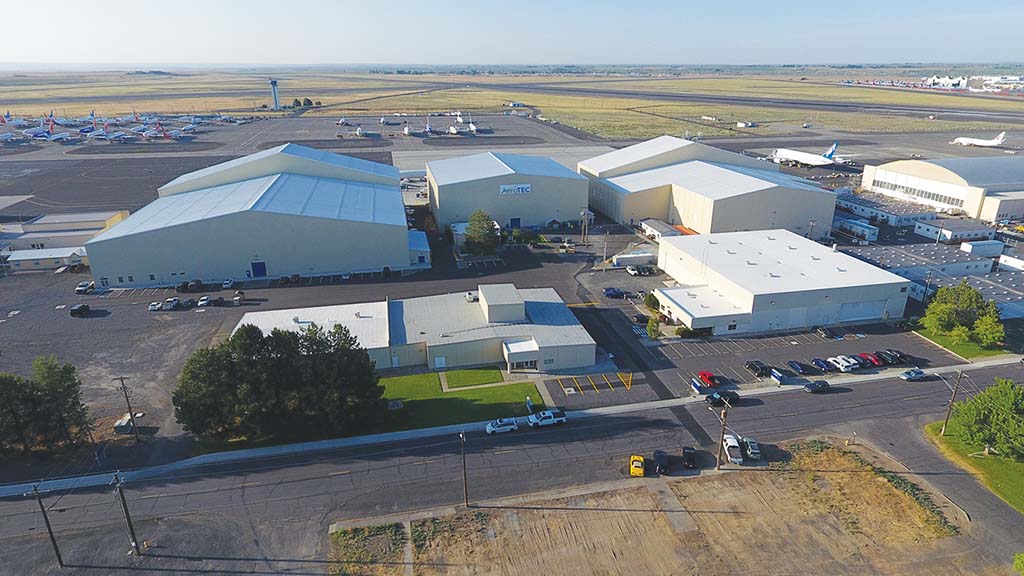
AeroTEC has been growing its MRO capabilities and facilities alongside its engineering business. It operates an FAA-certified Part 145 repair station in Moses Lake and opened its third maintenance hangar there in 2021. Between its two widebody hangars and one narrowbody hangar, AeroTEC has 182,000 ft.2 of space to perform MRO services.
Human says AeroTEC offers MRO services as a supplementary business, focusing on special mission or “one-off” aircraft most MRO providers would turn down due to concerns about profitability and turnaround times.
One-Offs
“[Special mission aircraft] have been highly modified and have a unique approved FAA maintenance program. To get access or to do the maintenance work often requires quite a bit of disassembly of the modified aspect of the airplane,” Human says.
Instructions for maintenance of these aircraft can also be significantly less clear-cut. “They may or may not have the detailed reference data that you might expect out of a Boeing maintenance manual supplement, where there are very clear instructions and a technician has done it 100 times before,” Human says. “These are one-off, bespoke tasks, and we are set up for that. We’re not afraid of that—we embrace that.”
AeroTEC also regularly collaborates in-house with customers’ maintenance supervising staff, technicians and mechanics to complete work. It has a series of trailers on-site that can be configured specially for a customer’s staff. “We recognize that because these are bespoke aircraft, they do require special handling, tooling and experience. We welcome those people to participate in the maintenance event because they know the aircraft better than anyone else,” Human says.
Currently, AeroTEC holds FAA ratings for Boeing 727, 737NG, 737 MAX, 747, 777 and Cessna C208B Caravan aircraft. It also holds engine ratings for CFM International CFM56s and Leap 1Bs; GE CF6s and GE90s; Pratt & Whitney PW4000s, PT6s and JT8D-17s; and Rolls-Royce RB211s and Trents. Human says it typically takes AeroTEC around 45 days to add a new airframe or engine type to its capability list. “Another MRO may not be willing to add a type to their rating list for one aircraft, whereas we will go do that,” he says. “There’s obviously cost involved in doing that, but we figure out the business case for that customer and the potential future business, and we’ll make that decision.”
Although AeroTEC’s primary maintenance focus is modifications, it also offers services such as A and C checks, heavy corrosion inspections, nondestructive inspections, lease returns and reconfigurations, battery repair and aircraft-on-ground services. If a customer’s aircraft requires maintenance services that AeroTEC cannot perform in-house, it subcontracts work or collaborates with its customers to bring in additional expertise as needed.
AeroTEC is also stepping up digitalization in its maintenance operations, Human says, including in its parts and paperwork processes. The company just released a major upgrade to its NetSuite software for inventory and parts management to increase efficiency, reduce errors, provide better visibility and enable technicians to search for and request parts and tools from mobile devices. Human says the goal is for tools to be brought directly to the technician on the floor. “We want the smart technicians to be working on the airplane, not standing in line at the tool room or parts counter,” he says. AeroTEC is also looking at how to incorporate “homegrown tools” related to work order management into NetSuite.
In addition to its Moses Lake flight-test center and Arlington manufacturing facility, AeroTEC also operates from its headquarters in Seattle and engineering facilities in Wichita. On the manufacturing side, the Arlington facility focuses on FAA-approved production parts, while Moses Lake primarily focuses on flight-test and support equipment.
“We’re not a Spirit AeroSystems. We’re never going to be doing high-volume, large-scale production, but where we do excel is the weird stuff—the things that are out of the standard process or prototype, where the customer only needs one or two,” Human says.