
Enrique Robledo, CTO, Iberia Maintenance.
Aviation Week’s AeroEngines Europe conference in Madrid in September explored issues and the outlook for the Pratt & Whitney geared turbofan and CFM International Leap engines. Here are some key takeaways from the event.
GTF in the Spotlight
The September announcement by Pratt & Whitney’s parent company RTX that it intends to ground 350 geared turbofan (GTF) engines powering Airbus A320neo aircraft annually from this year through 2026 not only further disrupts both current and future operators of the new-generation narrowbody, but also has consequences for MRO capacity and the availability of current-generation engine assets. Durability issues on the engine have led to groundings owing to parts and spare engine shortages. The engine market has already seen heavy disruption in recent years from pandemic production cuts and technical issues with not just the GTF but CFM International’s Leap engine program as well.
The GTF groundings will have an inspection timetable, likely making shops more busy. Iberia Maintenance says the GTF groundings will feed much of the initial capacity at its Madrid engine shop, where it plans to induct its first engine in either October or November after having gained approval for the narrowbody engine last year. Further afield, Pratt’s Eagle Services Asia joint venture with SIA Engineering Co. announced capacity expansions at its Singapore facility to accommodate more GTF work. The industry anticipates further capacity increases in the form of partnerships and added shop capacity. Pratt has 14 GTF-approved shops in its aftermarket network, while CFM plans to grow its own MRO network for the Leap to 20 shops in the next few years.
In the long term, the engine MRO segment expects the GTF will return to a competitive position once the OEM irons out the engine’s durability and parts issues. While concerns about OEM maturity testing during the program’s development phase were cited, the scale of the ramp-up is seen as the biggest driver of the program’s current challenges. “The issue is that the ramp-ups for the GTF and Leap have been so rapid compared to previous generations of aircraft that there are two orders of magnitude that have had a greater impact as a result,” says Keith Brown, group head of procurement for engines, MRO and aircraft interiors at International Airlines Group, parent company of British Airways, Iberia, Aer Lingus and Vueling.
Speaking in a panel discussion on new engine fleets at Aviation Week’s AeroEngines conference here, Brown says that while claims that airlines were somewhat naive in their risk assessments of not only the GTF but also the Leap engine program are valid to some degree, orders were dictated by the choice of just two engines in the new-generation narrowbody aircraft market. “If you needed the fleet, you needed to buy the aircraft to pick one of those two engines,” he says. While not finding it too soon for operators to abandon the program entirely, the panel agreed that a long-term change in which operators either order their engines separately or later and apart from their airframe commitments could be a possible long-term solution to address technical issues related to GTF and Leap engines.
Exploring How To Cut Lead Times
Turnaround times (TAT) in the engine segment remain unusually long compared with other parts of the industry. This has led MROs and airline maintenance facilities to try to bring more services in-house to cut lead times. In the wake of OEM parts cost increases and availability issues, along with soaring used serviceable material (USM) demand, MRO shops and airline maintenance divisions are turning to designated engineering representative (DER) repairs and parts manufacturer approval (PMA) parts to reduce TATs and increase affordability.
“Post-Covid it’s been a challenging environment not just from an operational sense but also related to raw materials as well,” says Alex Dulewicz, project director at Chromalloy. He categorizes three main areas the company is seeing in relation to parts shortages: first, source-controlled repairs sent back to the OEM and incurring additional TATs; second are parts awaiting raw materials with Dulewicz citing industry honeycomb shortages impacting its ability to turn around repairs within the contracted TATs, and third: replacement material but this can be offset by proprietary advanced repairs where a small repair TAT increase is favourable to the lead time on new parts. “… the intention is we turn a part that would otherwise be destined for the scrap bin into a serviceable part – these salvaged repairs can significantly increase yield rates,” he says.
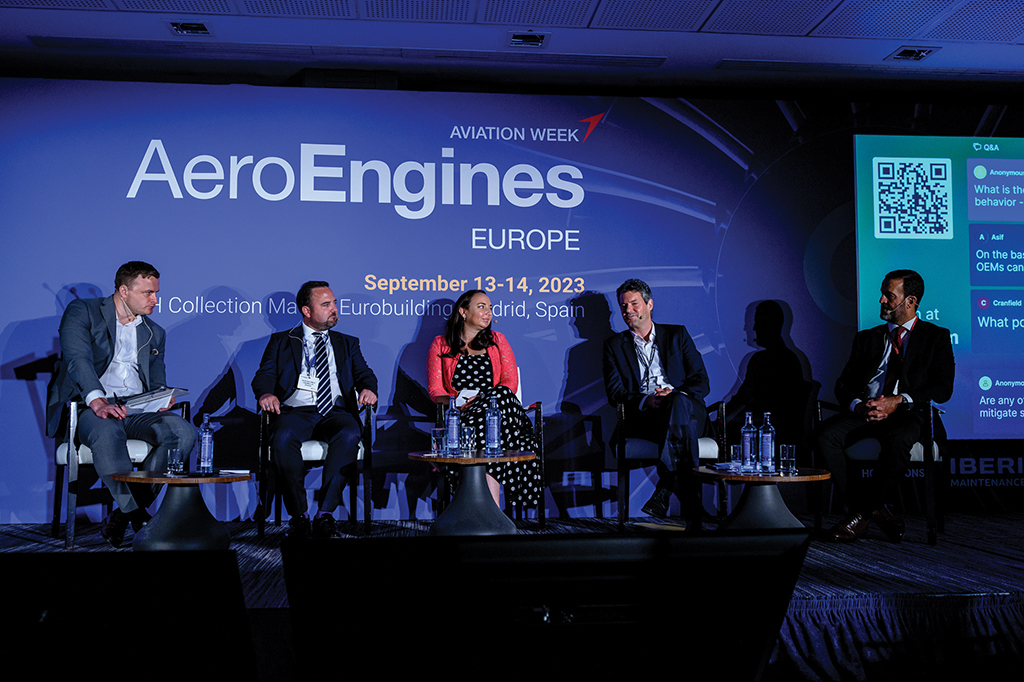
Dulewicz explains that Chromalloy leverages a suite of solutions to augment the existing supply chain and speed engines’ return-to-service. In addition to engine parts repair and PMA activities, Chromalloy can draw on its material services business based in Fort Lauderdale, Florida to overcome supply chain issues. “We can mitigate some of the challenges in terms of the extended lead-times that we are seeing through used serviceable material. We also have a strategy of putting exchange pools in place…” which he states provide the dual benefit of economics and readily available material to keep engines moving through shops.
Matthias Niessen, senior director for engine parts repair at German MRO giant Lufthansa Technik (LHT)—a company with GTF and Leap 1A and 1B capabilities—says it has seen a lot of repair demand for the more established IAE V2500 over the past year. He says the company has utilized its mobile engine service offerings to keep workscopes on engine maintenance small. “We’ve also used internal repair capability, especially related to nondestructive testing capability, to enable the quick-turn services needed,” he says. Niessen notes that LHT recently acquired additional ultrasonic equipment it will use to help address repair issues. The company had ramped up overhaul and repair capabilities for both the GTF and Leap engines but has adapted to change its plans, given the issues affecting both engine programs. “We have always looked to increase capacity and ramp up engineering manpower to be able to produce repairs and capability quickly aimed at solving the issues at hand,” Niessen adds.
Navigating the Supply Chain
With supply chain constraints still affecting the industry on a large scale, forecasting the need for parts required for engine workscopes has become more challenging for the engine MRO segment. While most shops will know which parts they are likely to require in the future, customer engine maintenance demands have shifted as obtaining parts from a constrained supply chain has become more problematic.
Ana Bidarra, engine shop planning and control manager at TAP Portugal, says demand placed on MROs is greater than the supply chain’s rate of recovery, and this makes engine shop planning more difficult. “It’s very hard to plan in advance because the type of work-scopes also changed a lot, because it’s customer-by-customer and changing the type of engines,” she says. She adds that close partnerships with customers are key to addressing these challenges. “This is so we know in advance what type of workscopes need to be done,” Bidarra notes. “We need to know the exact configuration of the engine order to have parts installed into the engine.” Lead times related to OEM parts continue to be a problem for TAP. “The strange thing is these are not just for larger parts, but also expendable ones,” she says.
Christophe Giraud, senior commercial director at AAR Corp., says he had never envisaged the reality of shop visits with TATs of 200-300 days. “When you have a life-limited part that once took 30 days to repair and now takes 90 days, that is a concern,” he says. However, Giraud believes some of the logistics issues would have occurred regardless of COVID-19, comparing the scenario to 17 years ago when he started in the industry and there was an abundance of parts stock to feed then-popular just-in-time material models. The industry is still suffering from factors outside its control, he says, citing the Russia-Ukraine war and rises in inflation levels and interest rates.
From an operational perspective, some MRO providers have reevaluated their parts inventory strategies. Ivan Gonzalez Vallejo, director for strategy and supply chain at Iberia Maintenance, says he has witnessed two parts-stocking scenarios in recent times. “You either stock up because you want to be a stockholder and therefore get some cover from issues with vendors, or the opposite, where a company de-stocks in order to generate cash flow,” he says.
Iberia has chosen to hold a bit more inventory, which Vallejo says is not an issue if that inventory is moving around, while it has also expanded in-house repair capability. He notes that good forecasting is important so companies can duly increase stocks and availability, adding that Iberia has enhanced its procedures for this through technology such as machine learning algorithms and artificial intelligence to help forecast planning. Vallejo also expects supply chain constraints to ease within the next 18 months.