
Using hydrogen to power aircraft is not a new concept—the first attempts began more than 60 years ago—but commercialization of the technology is getting closer to reality. As airlines face pressure to reach the air transport industry’s goal of net-zero emissions by 2050, more are joining innovative efforts to retrofit regional jets and turboprops with hydrogen-electric propulsion systems. Over the last year, a slew of airlines, OEMs and lessors have signed on to partnerships with hydrogen-focused startups to begin developing hydrogen-electric aircraft conversions.
One of the big players is ZeroAvia, which is developing multiple hydrogen-electric powertrains. These include a version to support smaller 5-20-seat aircraft, such as the Cessna Caravan and Dornier 228, and a version capable of powering 40-80-seat aircraft, such as ATR 42s and 72s, Bombardier CRJs, De Havilland Canada Dash 8s and Embraer ERJs. In addition to the sustainability benefits of a hydrogen-electric powertrain, ZeroAvia says these retrofits have commercial potential because they can extend the life and appeal of these airframes.
Among the operators backing ZeroAvia is Alaska Airlines, which invested in the startup under its recently formed venture capital arm, Alaska Star Ventures, as part of its plan to reach net-zero carbon emissions by 2040. It plans to donate a Bombardier Q400 to ZeroAvia that will be retrofitted with a hydrogen-electric powertrain in exchange for equity in the company. Although Alaska has since decided to phase out its Q400 fleet in favor of Embraer 175s, it still sees the project as a necessary step in its net-zero carbon strategy.
According to Pasha Saleh, head of corporate development at Alaska Airlines, the ZeroAvia Q400 conversion program will be an important learning experience. “This will be by far the largest hydrogen-electric aircraft in the world when we’re done with it, and that technology will serve as a learning point for how we retrofit regional jets going forward,” he says.
ZeroAvia and Alaska will be developing retrofit kits consisting of four main components that will require modification: the engine, nacelles, avionics and hydrogen tanks. Saleh says the gas turbine engines will be removed and replaced with the large electric motors that ZeroAvia is developing. Next, a power generation system that converts hydrogen into electricity will need to be installed along with hydrogen tanks. New avionics to manage and monitor these systems will also have to be installed in the cockpit.
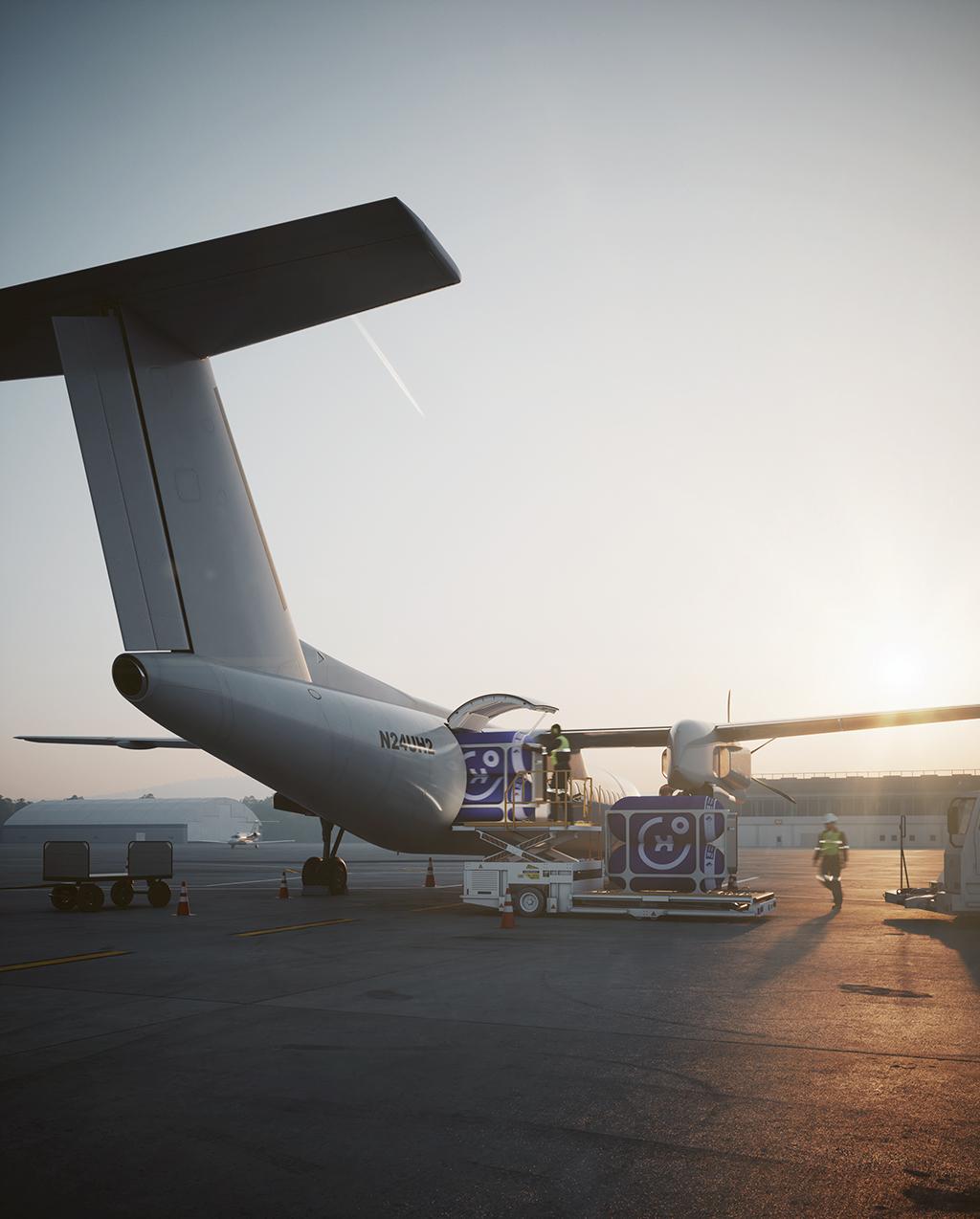
ZeroAvia has a number of similar agreements in place with other owners and operators of regional jets and turboprops. It says conversions will begin once its hydrogen-electric powertrains are certified and introduced to the market. The company is targeting 2024 for the smaller ZA600 powertrain, which will use gaseous hydrogen stored onboard in lightweight tanks, and 2026 for the larger ZA2000 powertrain, which will use liquid hydrogen.
Although ZeroAvia will lead these conversions, it will be drawing upon MRO expertise from partners including Alaska and MHI RJ Aviation Group (MHIRJ), which have experience maintaining the aircraft models set to be converted.
Saleh says that while Alaska’s own technicians will not be performing the physical modification work, they will be present to “draw on as a source of knowledge for working on these airplanes.”
MHIRJ will be helping ZeroAvia with engineering services, aircraft integration and certification support for the retrofit of CRJ700 regional jets. “We’re basically going to dovetail into ZeroAvia’s road map and strategic view to support them on the technical intricacies of being able to take a hydrogen concept and . . . industrialize and scale that so that, operationally, it becomes viable,” says Elio Ruggi, senior vice president and head of aircraft development and quality at MHIRJ.
As a specialist in CRJ MRO, MHIRJ wants to position itself to support future hydrogen-electric conversions. “A lot of the startups will have the innovators, but they won’t have the engineers who have practical hands-on experience in certifying, designing and testing aircraft, and that’s what [MHIRJ’s] Aerospace Engineering Center can do,” says Ross Mitchell, vice president of communications at MHIRJ. He adds that its work with ZeroAvia could benefit all regional aircraft, not just the CRJ.
Also focused on these types of conversions for regional aircraft is Universal Hydrogen, which has publicly signed letters of intent with eight airlines and lessors. Chief Commercial Officer Rod Williams says Universal Hydrogen also is in talks with “close to 60” airlines around the world. The startup is working on a supplemental type certificate (STC) to convert ATR 72s and Dash-8s to hydrogen power. The technology will use a hydrogen fuel-cell powertrain to replace the turboprop engine as well as install control systems, compressors and a thermal management system.
A core component of the Universal Hydrogen conversion method revolves around its modular hydrogen capsule technology, which will be used to both transport hydrogen to and from an aircraft and to hook up with and fuel the aircraft.
“This technology is a critical enabler to make the whole solution work, because what has prevented hydrogen aircraft from being commercialized in the past is the fact that there’s no infrastructure to transport hydrogen all around the world,” says Williams. “Instead of building hydrogen pipelines, specialized hydrogen tanker trucks, on-airport storage and in-tarmac pipelines for hydrogen, the key enabler is the module, which allows you to ship hydrogen to the airport and onto the aircraft at any airport in the world.”
Integral to the conversion, flight testing and certification of Universal Hydrogen’s Dash-8 retrofits is modifications specialist AeroTEC. It has set up a Hydrogen Aviation Test and Service Center at Grant County International Airport in Moses Lake, Washington, alongside Universal Hydrogen and its partners, Plug Power and MagniX, which are supplying the aircraft’s fuel cells and electric motor, respectively.

AeroTEC has worked on several electric aircraft conversion projects over the last few years, but CEO Lee Human says the Universal Hydrogen project will be its first opportunity to do the recurring manufacturing, kitting and modification work. “We have learned and continue to learn a tremendous amount around what it means to retrofit an aircraft and what it means to certify a clean-sheet electric aircraft,” he says. “We’ve learned a lot about high-voltage electronics, battery systems, battery management, battery cooling, propulsion, motor cooling and things that you don’t think about.”
As with other advanced air mobility platforms, these hydrogen-electric aircraft will demand a new set of required technician skillsets and maintenance considerations. “All of our technicians that work on these aircraft have to go through high-voltage training. We are dealing with 800-1,000 volts of electricity—and that can kill you,” stresses Human. “Hooking up the battery systems is a new trade. It’s a function of an aircraft maintenance technician, but it’s never been contemplated in their coursework. When you go to A&P school, you don’t learn about hooking up 1,000-volt battery systems, so we have to supplement that.”
AeroTEC is tackling this challenge by introducing new curricula, training and safety equipment. “I think there are some efforts to take learnings from eVTOL groups and companies like AeroTEC and really start a knowledge base of best practices,” says Human. “We do quite a bit of sharing with some of the test organizations that we are members with.”
Universal Hydrogen’s Williams points out that the hydrogen-electric retrofits will certainly require changes to maintenance activities. “The area that would change the most is the powertrain, because you’re taking a turboprop engine, which has a clear set of inspections and maintenance activities, and you’re replacing it with a completely different type of powertrain, which is based on electric motor and fuel-cell technology,” he says.
Williams also notes that Universal Hydrogen has received “quite a lot of interest” from global MRO shops interested in getting in on the ground floor of hydrogen-electric aircraft projects.
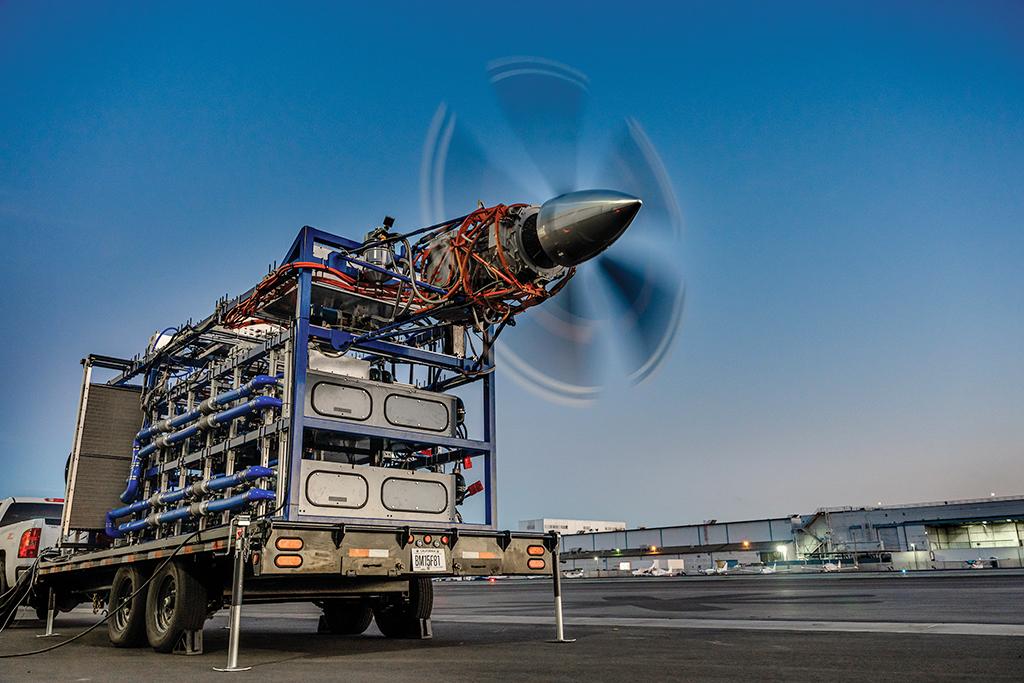
One MRO that is already taking steps to prepare for hydrogen is Lufthansa Technik (LHT), which launched a project last year alongside the German Aerospace Center, the Center for Applied Aeronautical Research and Hamburg Airport to design and test processes to handle hydrogen technology. The project will feature both a virtual and a physical component. It will transform a decommissioned Airbus A320 into a “stationary laboratory,” using liquid-hydrogen infrastructure and creating a digital twin to research digital health monitoring and predictive maintenance.
LHT’s technicians will be installing a range of components on the demonstrator A320, including an internal cryo-tank for liquid hydrogen, a fuel-cell system, a conditioning system and various pipes and interfaces. The project partners will also be setting up ground infrastructure such as external storage for liquid hydrogen.
According to Gerrit Rexhausen, Lufthansa Technik’s manager of corporate innovation and project lead for the Hydrogen Aviation Lab, the MRO is focused on aspects such as time-efficient hydrogen refueling, safe and efficient repair of components, and figuring out how to deal with potential incidents.
“With today’s technology, refueling a long-haul aircraft [with hydrogen] could take about as long as a flight from Europe to the U.S.,” says Rexhausen. “How can we speed up refueling in the future to the point where it enables practicable turnaround and handling times on the ground? And how do we avoid overfilling or wasting hydrogen during refueling?”
Storing the hydrogen in liquid form will require cryo-tanks, which cool it to -250C (-418F). Rexhausen says this will require figuring out not only how to accomplish this cooling but also how to protect components, aircraft systems and ground workers from these temperatures. He identifies several questions the project will need to address in this area: “Will the new technology bring certain no-step or no-touch areas for maintenance personnel? Do MRO technicians have to wear special protective gear to be able to work on cryo-cooled components?”
Aside from cooling complications, liquid hydrogen has several other pitfalls that LHT is trying to manage. Hydrogen can “boil off” and become gaseous again due to ambient heat, so LHT wants to figure out how to avoid this as well as how to recapture and reliquify boil-off gases. Hydrogen is also combustible, so it will need to be inerted when stored on the ground and in the aircraft. “Especially for the MRO of hydrogen components, it is essential to have suitable procedures and protocols in place here, as well as appropriate preparation and follow-up, so that all necessary maintenance work can be carried out safely,” says Rexhausen.
Despite these challenges, hydrogen-electric aircraft could also simplify maintenance in some ways. “Interestingly, and maybe somewhat counterintuitively, we expect that the future implications are that engine maintenance will be easier,” says Alaska’s Saleh. “There will be no high-temperature alloys because there’s no hot section of the engine that takes all the wear and tear. There are fewer rotating components, and anytime you switch to electric versus combusting something, there’s less wear and tear.”
Saleh says these lower repair requirements could play a big role in the economics of proving that hydrogen-electric flight is commercially viable. However, he remains skeptical that these types of conversions could ever be commercially viable for narrowbody and widebody aircraft—in part due to some of the cryogenic challenges LHT is trying to resolve.
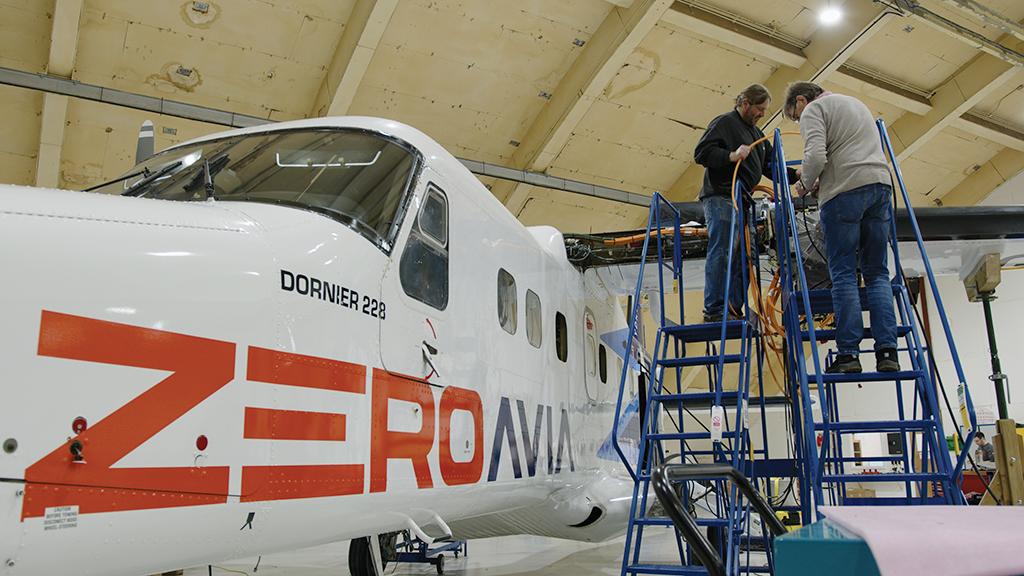
its ZA600 powertrain is certified. Credit: ZeroAvia
“To use hydrogen to power larger airplanes like that, it would have to entail actually combusting the hydrogen,” which would require cryogenic hydrogen stored at extremely low temperatures, says Saleh. “You’re talking about converting these aircraft to being a flying refrigerator.” He mentions Russia’s experimental Tupolev Tu-155 alternative-fuel testbed from the 1980s, which operated on hydrogen and, later, liquid natural gas, noting that it was “all just filled with tubes and refrigeration,” with no room for passengers or seats. Instead, Saleh believes sustainable aviation fuel will be key for alternative propulsion for larger aircraft—at least in the near term.
AeroTEC’s Human shares Saleh’s skepticism about the viability of hydrogen fuel for larger aircraft “until there’s a discovery.” He adds: “Some of the expectations are aggressive in some of the press releases I’ve seen from others, but we’re making really good progress toward real, commercially viable green aircraft.”
Williams says Universal Hydrogen sees ATR 72s and Dash 8-300s as ideal to start with, since they can be powered by fuel-cell technology. “As you get into bigger, more powerful aircraft, you would actually need a hydrogen-combustion engine, which would require the main engine OEMs to develop a hydrogen-combustion engine,” he says. Under Universal Hydrogen’s development plan, “all the technology is under our control, which means we can control the timing and get to market as fast as we possibly can,” he adds.
Despite these challenges, ZeroAvia is targeting larger classes of aircraft. “Our mission is a hydrogen-electric engine in every aircraft,” says ZeroAvia’s vice president for Europe, Sergey Kiselev. “We have a road map up to narrowbody jets that we think is achievable over the next 15-20 years. The largest, widebody aircraft may be further in the future, but we know fundamental limits. Hydrogen will be a bulkier fuel, and as we get significantly above 100-seat aircraft, clean-sheet designs will be needed to find optimal ways for housing the fuel tanks.”
Another hurdle these projects will need to clear is achieving regulatory certification.
“What’s going to be exciting is how we’re able to influence evolution of regulation,” says MHIRJ’s Ruggi. “If you open up the certification requirements from the FAA, Transport Canada or NASA, you won’t find a clear road map to fuel- cell certification, so the rules will evolve and adapt. [This will] create opportunities for other incumbents in the industry to also contribute to the success of hydrogen in our future road maps.”
However, Human says so-called more electric aircraft such as the Boeing 787 have helped to pave the way for certifying hydrogen-electric aircraft. “The certification road map is the same whether you’re certifying a winglet, a cargo door or an electric aircraft. The devil’s in the details—so [it’s about] the applicability of certain regulations and the interpretation of those to what we’re bringing to the table,” he says.
Based on AeroTEC’s previous experience with electric aircraft conversions, Human estimates that the time frame from initial design to certification could be 2.5-5 years, depending on whether the project entails a major modification or a clean-sheet aircraft.
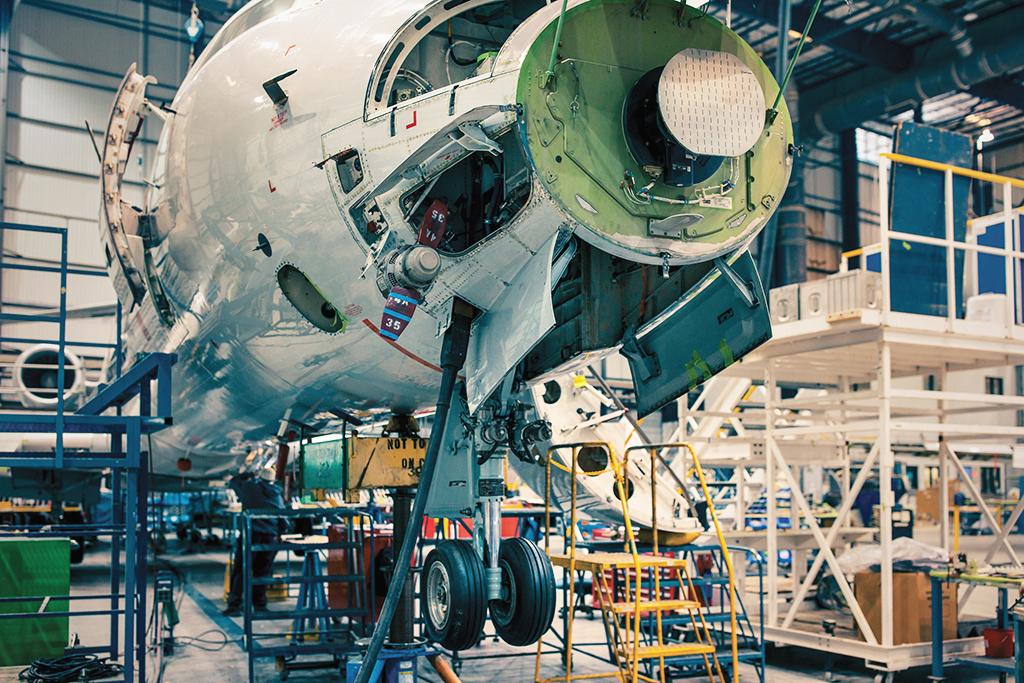
Williams says Universal Hydrogen is still figuring out the details of what the conversions will entail and how long they will take, but the scale of the projects will not be unprecedented. “I would consider it to be . . . comparable to what many MRO shops do today when it comes to taking a passenger aircraft and converting it into a freighter aircraft. There are many STCs for many different types of aircraft which exist today to do a conversion like that,” he says. “I don’t know where we’ll end up in terms of the amount of work to do the conversion, but it’s going to be on the scale of some of those similar types of cargo conversions which happen today.”
Williams notes that Universal Hydrogen is also still working to establish its partner MROs for modifications. “We’re pretty agnostic when it comes to that, and the position that we’ve taken is we’ll work with the airlines that are purchasing the conversion to determine which of the MRO shops the airline would prefer to work with,” he says.
At ZeroAvia, work is expected to start in 2024 on the first ZA600 conversion. “After that, larger airframes will be equipped with hydrogen-electric powertrains as the market gets traction and experience, and novel airframes capable of carrying light but bulky hydrogen will be created and put into operation in the 2030s and 2040s,” says Kiselev.
“We’re taking a really scientific and disciplined approach to this,” notes Saleh. “There’s going to be a full year of engineering and design work before any metal is cut or before anything is removed from the Q400.”