MROs Look Beyond The iPad For Digitalization Road Map

Despite efficiency benefits from introducing tablets to the hangar, connectivity issues and unstructured data have created challenges for Lufthansa Technik.
From line maintenance on the apron to heavier maintenance in the hangar, the MRO sector is increasingly relying on individual electronic devices to schedule, assist with and even certify work. By and large this means using tablets, but larger-format smartphones also have been used in this space.
The benefits are many: making better use of technicians’ time, increasing efficiency across the organization, reducing turnaround times, increasing transparency and boosting overall customer satisfaction—all with less physical paperwork.
But what have been the biggest wins from the tablet revolution, and what is next on the technology road map?
Reaping Benefits
“Tablets and other mobile devices on the shop floors of Lufthansa Technik significantly change the way we conduct our MRO business,” says Claudia Nehrke, head of digital transformation and strategy at Lufthansa Technik. “They form the cornerstone of our digital shop floor management undertakings and serve as a tangible manifestation of our company’s digital transformation. Tablets replace the paper-based legacy processes, enabling our mechanics to access and process all necessary data right at the workbench.”
Technicians no longer need to juggle job cards, manuals, guides and other paper formats of documents. Everything they need to organize themselves, schedule work, carry out tasks and submit them for approval is on the device.
“Overall, this digital shop floor dramatically reduces turnaround times and error rates,” says Nehrke.
It is not just about speed—it is also about quality.
At the gate and on the apron, United Airlines has seen dramatic improvement in the efficiency of maintenance and repair work following implementation of tablet technology.
“A major benefit was the ability to release aircraft planeside,” says Diana Krohn, managing director of digital fleet management at United. “With a last-minute maintenance issue, every minute counts. For example, we shaved off three minutes of our short delays because technicians were able to complete paperwork digitally and didn’t need to go back to a computer workstation. As our mobility journey continued, we eventually made nearly all computer-based tasks accessible via the iPad, reducing travel time, eliminating paper and increasing frequency of updates.”
Specifically, Krohn says, “our custom software allows us to audit paperwork in real time, providing in-the-moment accuracy before releasing the aircraft. This process eliminates the need to have a manual review, which sometimes includes shipping paper back to a records team. Additionally, we are able to make assignments, order parts and reference manuals all from the iPad.”
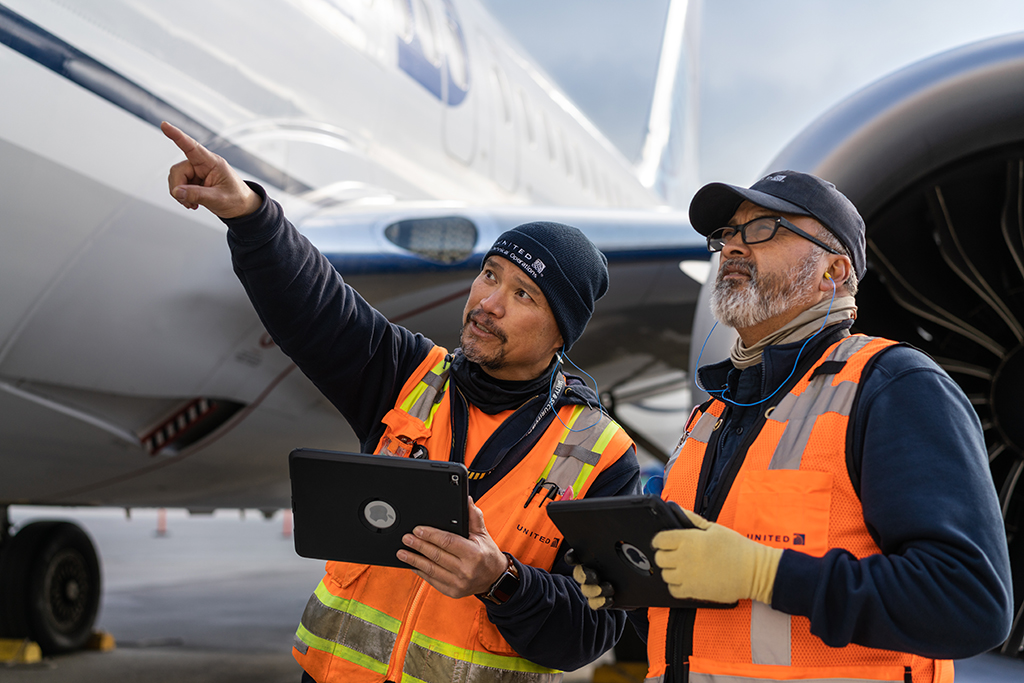
United realized an unexpected benefit of its tablet-based system during the height of the COVID-19 pandemic, when maintaining physical distancing was a business-critical requirement. The airline was able to conduct distanced shift briefings via the tablets, keeping key maintenance staff safe and healthy during the pandemic.
In addition, Krohn notes, “we’ve also [discovered] that techs can directly connect with experts in different stations, offer support and communicate more precisely with photos through this program.”
At a time when the industry is suffering from a lack of technicians, being able to use senior staff expertise more efficiently is a clear and easily realized benefit.
Tablet Troubles
Despite the obvious benefits, transforming what has traditionally been a greasy-fingered, overalls-and-tools business into a digital-enabled one has not been without its challenges. This extends beyond finding an oleophobic coating so technicians with greasy fingers can use touchscreens without needing to wash their hands.
Beyond skilling, upskilling and reskilling staff, Nehrke says there are two main challenges to introducing tablets and other mobile devices into the hangar. “For one, as airplanes naturally act as Faraday cages, connectivity issues were a key problem we had to deal with after launch, with Wi-Fi availability inside the aircraft on the shop floor being severely constrained,” she says. “To overcome this challenge, Lufthansa Technik has since pioneered innovative shop floor-based private 5G networks to avoid the physical limitations of Wi-Fi technology.”
Nehrke says the second challenge is that much of the critical data required for shop floor MRO has historically been available in an unstructured and sometimes closed way—either on purpose to guard intellectual property or simply because there has never previously been a business requirement to structure it for this kind of use.
“Consequently, improved data availability on the shop floor—thanks to tablets and other mobile devices—does not immediately yield tangible benefits,” says Nehrke. “We are solving this challenge head-on by leveraging our expertise in artificial intelligence and natural language processing technologies to turn unstructured data such as manuals into structured information that can be readily leveraged in the form of convenient, bite-size data such as task sequences on job cards.”
Ensuring certification approvals and compliance in a sector previously dominated by extensive physical paperwork has also been a challenge. An aircraft changing operators or owners with its baggage hold seemingly half-filled with maintenance and certification documentation remains a common occurrence. While this has complicated designing, agreeing to and implementing digital sign-offs and certification of work, the process has accelerated recently.
“United is the first airline to get approval from the FAA to digitize maintenance release documents using Touch ID on iPads,” says Krohn. “Overall, the tablets have fundamentally changed how our technicians interact with technology in their day-to-day workflow.”
Deploying Updates
Moving to a tablet-based model for MRO operations is not just about the hardware. Developing, iterating and updating the software that devices used for MRO need has been a critical part of the process.
Krohn says “the iPads provide a platform to deploy our custom applications, which are rapidly updated to keep pace with our developments and ever-changing business. For example, we are able to deploy analytical models to the custom applications.”
Nehrke concurs: “Perhaps the most significant aspect of our digital-transformation journey that has been catalyzed by our introduction of tablets on the shop floor has been our ever-increasing use of highly data-driven planning and steering software. Just five years ago, it was impossible for mechanics to have more than static job cards and maintenance data available to them, with such data historically only being available on paper when on the job.”
The benefits are many, including continually updating operational and error analysis, which can combine historic information with operational experience to provide valuable insights.
Process improvements are also enabled, both within the shop and with customers. No longer must owners and operators show up at the hangar to conduct visits—even technical ones. They have live status reports, can perform approvals and releases with the connected systems, and, if needed, can carry out virtual inspections via video conferencing solutions from wherever they are in the world.
Looking Beyond the Tablet
Just as the everyday use of tablets is the science fiction of the past, the science fiction of today is the operational normal for the future. This will be as true within the world of MRO as it is elsewhere—and the future is approaching rapidly.
“We are already striving to go beyond tablets and other conventional mobile devices, and aiming to make our shop floor environment not just keyboard-less, but even screen-less,” says Nehrke. “In doing so, we envision a truly digital shop floor, with operations planning and enhanced material and asset management forming one cohesive, hands-free experience for our workforce.”
Aviation has always been at the forefront of simulation technology when it comes to pilot training, but its benefits are increasingly rolling out to the MRO world as well.
These include, Nehrke says, “enabling mechanics to get a first impression of certain types of aircraft before they can be made available at their training location; this is especially convenient when new types of aircraft become available. This will allow us to realize significant time and cost improvements in the training of mechanics for our growing business, all the while ensuring the high quality of services our customers rely on. As with all new hardware introduced to our MRO operations, this technology will not only provide short-term operational benefits, but will also enable us to speed up the digital transformation of Lufthansa Technik.”
The use of virtual, augmented and mixed reality is beginning to edge past early proofs of concept and trials into actual reality on the hangar floor. Voice-based controls, too, are becoming increasingly reliable in many contexts, including those with strict safety requirements, of which MRO is just one.
Taken together, Nehrke explains, all this “forms a central part of our company’s digital transformation. The goal of our digital-transformation strategy itself is to digitally transform our internal processes across the entire value chain, and to make us a truly digital MRO company. With the initiatives we are undertaking today, we are already setting the stage for further digital transformation and new digital business models in the future.”
This wider digitalization of aviation—often collated as the group of technologies called Industry 4.0—means that the connected MRO workshop is becoming an indispensable part of the industry. Applying artificial intelligence, including machine learning and deep learning, to the expansive data pools that aviation collects will enable critical patterns to be identified via algorithm as well as with human expertise.
Digital twins, modeling, virtualization and visualization will also continue to evolve from beyond the expensive pieces of equipment where they were first introduced to the aviation context. From conceptual design to process work, logistics operations to supply chains, these technologies will also enable single points of truth to be visible, live via application programming interfaces, to everyone involved with the aircraft, from owners and operators right on down the value chain.
A crucial next step is the integration of the new generation of connected aircraft to aviation intranets and, indeed, the wider internet. As with much of aviation, the pandemic proved an accelerator, with the retirement of older aircraft and the need to optimize operations during a staffing crunch meaning that the industry finished the pandemic downturn with a substantially more modern fleet than the one with which it started.
For several years prior to the pandemic, aviation was promised an almost magical future of information flowing automatically from new, “smart” aircraft. Everything from engine sensors to connected coffee pots would automatically communicate their working/not working status (or in some cases, showing signs associated with failure) live from the aircraft. Automated parts logistics would dispatch a part from a warehouse to be delivered to the gate for a technician, assigned by a maintenance scheduling system, who is waiting to make the repair with maintenance instructions on their tablet or smart glasses, depending on the new technology in question.
Predictive maintenance would not only know the calendar schedule on which every part is likely to be replaced, but would have individual sensor-enabled component use cases. If a particular table is being raised and lowered in quick succession, that might mean it is broken. If the closest oven to the aisle accumulates use cycles at twice the rate of the one on the far side, it may need to be serviced or replaced earlier. Even data analytics that can track the extent of a component behaving in a certain way for a period of time before failure can be integrated and used for predictive maintenance.
This future is not quite here yet, but it is closer than the industry might have thought even a few years ago.