Opinion: MRO Robots Still Require Human Oversight
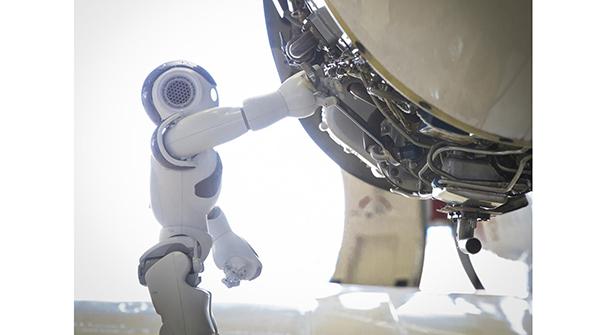
ARSA argues that the “robotics revolution” will still require human ingenuity for functional operations.
At ARSA’s Annual Conference in March, our aviation audience got to learn from the automotive community.
The association has long urged its members to see aerospace within a larger ecosystem of technical talent. It’s easy to see the “outside” purely as competition for workers rather than an opportunity to grow. To demonstrate that opportunity, we went in search of non-aerospace career development stories that could help us to improve recruitment and training.
That search paid off in the form of Gardner Carrick, vice president of workforce solutions at the National Association of Manufacturers (NAM). Carrick introduced ARSA’s conference attendees to the Federation for Advanced Manufacturing Education (FAME). Developed by Toyota, FAME combines classroom instruction, skills training and hands-on professional experience for young technicians.
“FAME inducted apprentices into three days of work and two days of classes at a partner college,” Aviation Week contributing editor Henry Canaday wrote in his report on the presentation. “Companies also deploy a mentor to ensure nontechnical skills and behaviors are learned as well. . . . Even during COVID-19, all participating companies thus stuck with the program. Some colleges say FAME has changed their entire approach to career education.”
The nuts and bolts of the program are instructive for anyone needing technicians, but there’s something else worth noting. Toyota started the program to produce multifunctional maintenance specialists for maintaining factory equipment, not to work on the products those factories turned out.
Looking forward to the “robotic revolution,” advancing technology will only shift the demand for human attention. Complex systems need oversight, even as they replace certain functions previously performed by a person. The ongoing-as-I-write-this speculation over how long Twitter’s social media platform can operate without engineering fixes is a case in point: Whether you’re posting a hashtag or troubleshooting a full authority digital engine control, the system only operates if a person can tend to it. As the brilliant minds at both Toyota and Carrick’s colleagues at NAM demonstrate: Keeping an “automated” facility running demands human ingenuity.
We make good on this understanding by investing in critical thinking. Like the new 14 CFR Part 147, which was also announced at the ARSA conference, our standards should be based on performance or competency rather than adherence to specific curricula or tool usage. Employers must think openly about career pathways and training strategies based on non-aviation experience. Governments must recognize how often the plain language of existing rules can embrace new technologies or business strategies.
Regardless of the new systems and technologies that arrive in aerospace facilities, aircraft will be maintained to the standards of the aviation safety rules. Meeting those standards is the work of smart and capable people; investing in their futures is the key to building the industry’s.
Brett Levanto is vice president of operations of Obadal, Filler, MacLeod & Klein managing firm and client communications in conjunction with regulatory and legislative policy initiatives. He provides strategic and logistical support for the Aeronautical Repair Station Association.