
Latecoere’s Elcocos project for aircraft doors targets faster manufacturing and the use of fewer raw materials.
With weight savings at the top of the list for any aircraft clean-sheet design or modification, cabin doors present yet another opportunity.
Lighter cabin doors can be achieved starting at the subcomponent level, says Satish Narayanan, vice president for engineering and technology for advanced structures at Collins Aerospace. He reports that while Collins has produced a limited number of passenger, cargo and auxiliary doors over the years, its current focus is on door subsystems such as emergency passenger assistance, flight lock actuation, sensors, lights, the electronic control module and evacuation slides.
Narayanan says Collins is incorporating weight savings into all of its design decisions, with a 20% weight-reduction goal for future door systems. “For example, by designing the evacuation slide, structure and mechanism together, it’s possible to achieve compact and efficient designs that weigh less and open more space in the fuselage,” he explains. “By optimizing the overall system architecture and subsystems at the same time, duplicate features can be eliminated.”
Reducing the weight of the subcomponents has a ripple effect. “When the door is lighter, the mechanisms and hinges can also be lighter since they don’t have to support the weight of a heavier door,” Narayanan says.
MANUFACTURING TRENDS
At the same time, he notes that significant weight savings are also being realized by using thermoset or thermoplastic composites. Collins sees these as “a trend for structural applications,” he says, specifically to the door skins and stiffening frames.
“This is a trend which is on the rise,” Narayanan says. “The Boeing 787 and Airbus A350 already use composites in their structure, and going forward, we see the use of thermoplastic composites increasing because of their improved toughness. This makes them more durable in an environment where impact from luggage handling or other airport operations can be frequent.” He adds that parts of the internal door mechanism could be fabricated from composites, citing the moving shafts that facilitate locking and unlocking.
Using fewer parts also reduces weight; employing thermoplastic welding in the manufacturing process would reduce the number of fasteners required, Narayanan says. “Alternatively, by using thermosets, more of the structure could be manufactured as one piece, cutting the number of parts and fasteners required for assembly,” he notes. “We are looking at simplifying the mechanism by reducing gears, cams and shafts. By balancing trade-offs between subsystems, we’ve come up with an approach that reduces the requirements for those parts.”
Asked about some of the areas where new door designs are likely to trend, Narayanan says opportunity exists for new variants where additional emergency egress doors might be added, as well as in the freighter conversion realm. “There will be more model-based systems, engineering-based design and development to optimize the system as a whole and more integrated components, embedded intelligence and composite structures,” he says.
Although composite doors do not have a maintenance advantage over doors fabricated from metal, according to Narayanan, he reports that there are other approaches to reducing maintenance. “We are looking at ways to connect the multiple systems, as well as a common health monitoring approach that can relay information digitally to the operators,” he explains. “This way there is no need to disassemble portions of the door.” Narayanan cites the pressure check of the evacuation slide pressure bottle as an example that in many cases requires partial disassembly of the door.
“Our team is also looking at ways to combine multiple sources of data from the door, the aircraft and the flight environment to add predictive health and optimize maintenance schedules to reduce aircraft downtime,” he adds.
THE COMPOSITES FACTOR
While composites may be no more durable than metal, Dirk Trott, chief engineer of passenger doors at Airbus Helicopters, says composite materials for the primary structure represent the most significant change to the current generation of cabin doors. Airbus Helicopters manufacturers most of the doors for Airbus commercial airliners, in addition to the OEM’s helicopters.
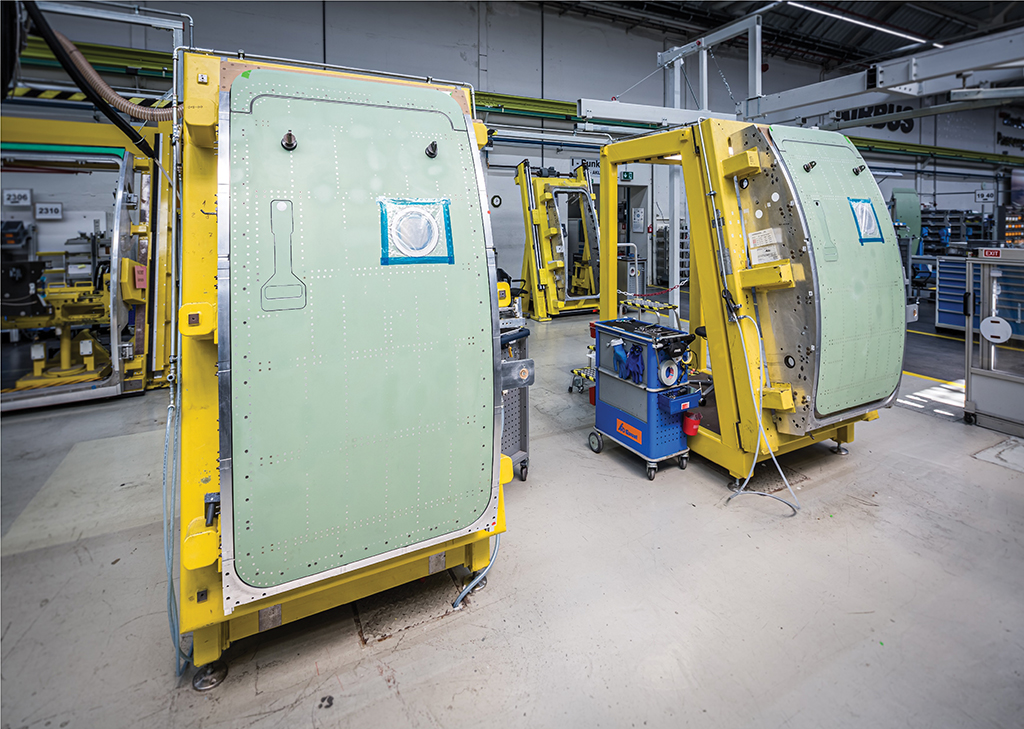
“The application of composites [to the cabin doors] was driven by weight-improvement targets compared to metallic structures,” Trott says. “Composites have a favorable ratio of high strength at low weight, which is why primary structural elements of the cabin door that carry flight and pressure loads are being manufactured from composites. These include the outer skin as well as the internal stiffening framework of frames and beams. In addition, composite material has proven to be a weight-effective material for the production of the main hinges for doors that are swiveled to open.”
Trott says improvements aimed at sustainability as well as operator and passenger comfort were achieved for thermal and acoustic insulation, along with maintenance reduction for systems integrated into the door. “Maintenance intervals for composite doors are comparable to—or longer—compared with the metallic doors,” he says. “But this has been a design target from the conception of the product and is achieved by application of respective sizing and corrosion protection principles.”
Trott says a key factor with cabin doors is the design of parts with a high integration level in tandem with reduction of single parts and related connections and fasteners.
“Parts reduction and higher parts-integration levels are design goals that are always pursued,” he stresses. “Recently, the most significant improvements for this were achieved by the use of 3D-printing/additive-layer manufacturing (3D/ALM) for metallic door operating mechanism assemblies, which allowed a reduction of single parts by almost 50%. In terms of production technology, 3D/ALM, especially with titanium, contributes to the improvement of weight, and is also a very important measure for the future.”
Trott says Airbus Helicopters has also addressed the risk of damage to cabin doors. “By far, most of the reported damage to cabin doors originates from support equipment such as passenger bridges and catering trucks colliding with door edges,” he notes. To increase door damage tolerance, the OEM has introduced “metallic protection profiles” around the outer perimeter of the composite door skin that deform when struck but prevent damage to the composite skin up to a defined load or impact level.
Looking ahead, Trott says the focus on low weight will continue to prevail. “Cabin doors have to fulfill two very opposite functions: staying safely closed and locked [while enabling] the operator to open them reliably under all normal and emergency conditions,” he notes. “Engineers are considering further weight reduction and use of composite structures that will allow high-strength designs that are able to accommodate both functions safely.”
INNOVATIONS
Along with part-count reductions and higher integration levels with composite structures, Trott says there will be further focus on noise reduction and better thermal insulation of the door. “Actuation will also be an area of interest, even though hydraulic/pneumatic actuation continues to provide reliable weight and cost-effective performance with long lifetime and low-maintenance efforts,” he explains. “However, simplification of door operation by application of electric actuation systems is a further field of development that is expected.”
Latecoere, a major supplier of aircraft doors, launched a promising technology applicable to cabin door manufacturing in 2019. A small demonstrator door dubbed Elcocos (enhanced low-cost complex composite structure) was delivered to Airbus in June 2021. According to Stephane Bouzat, Latecoere’s head of innovation and research and technology programs, the main innovation in the door’s manufacturing process involves the implementation of one single part for the main portion of the door, including the skin and the stiffening edge frame.
“The second main innovation is the capacity to consolidate the whole door structure in one shot with a dedicated curing mold, allowing fast door structure manufacturing and less raw material—composite and all additional film and textile traditionally used for infusion processes,” he explains.
Bouzat says Latecoere is using liquid-resin infusing technology for the Elcocos project. “Its advantage is in the competitiveness of the manufacturing, depending on the type of product and program rate,” he says. “However, in certain aircraft configurations, this technology allows the aircraft to improve its technical and economic performance, including weight, with the related benefit of CO2 reduction.”
While technology continues to enable innovations in door design, manufacturing and sustainability, Latecoere has also turned its attention to the real-world interface between the cabin doors and airline cabin crew. “A big improvement in door handling has been made possible by better understanding the cabin crew environment and getting their direct feedback,” says Thierry Eftymiades, Latecoere’s senior vice president for engineering.
For instance, Eftymiades says the door handles are sized by taking into account “ergonomics aspects” as they apply to any sample of the population as well as door interfaces and operating loads. “Based on past experience with mechanism sizing, Latecoere is able to propose better low-handle loads by considering all contributors, including seal effect, weight compensation and mechanism-securing means,” he says.