New Cabin Windows Seek Size, Efficiency, Sustainability Improvements
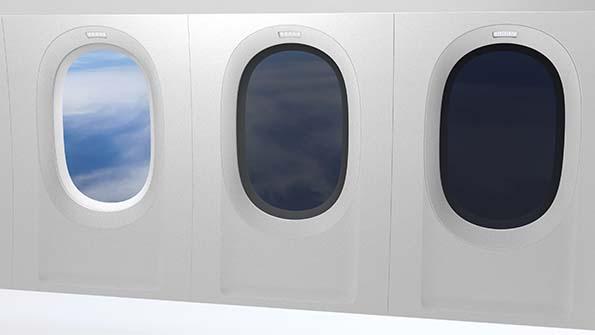
Gentex’s Gen 3 cabin windows are faster-dimming and darker than its previous Gen 2 windows.
If there are any ways to describe the current trends for passenger cabin windows, they must include the words “larger,” “longer-lasting” and “state-of-the-art.” Passengers today want not only a better visual experience but greater at-seat control over the level of outside lighting.
“I think there definitely is a trend toward larger windows on new aircraft types, and I suspect that will continue,” says Gary Weissel, managing officer of Tronos Aviation Consulting. “I also believe we’ll continue to see dimmable windows.”
Weissel explains that there has been substantial research involving the use of coatings applied to the exterior of aircraft windows to help prevent crazing (micro-cracking), too. “One of the airlines I’ve spoken with said that this was a major issue, and there were a variety of sealant/protective coatings on the market and in development, with some working better than others,” he notes.
Mike Behm, director of business development for Gentex, says cabin window technology developments will hinge on the use of lower-cost materials and processes, lighter-weight substrates and durability. “In order to achieve this, the alternatives could include a novel glass substrate or plastics with added layers and barrier films, specially treated to improve durability,” he says.
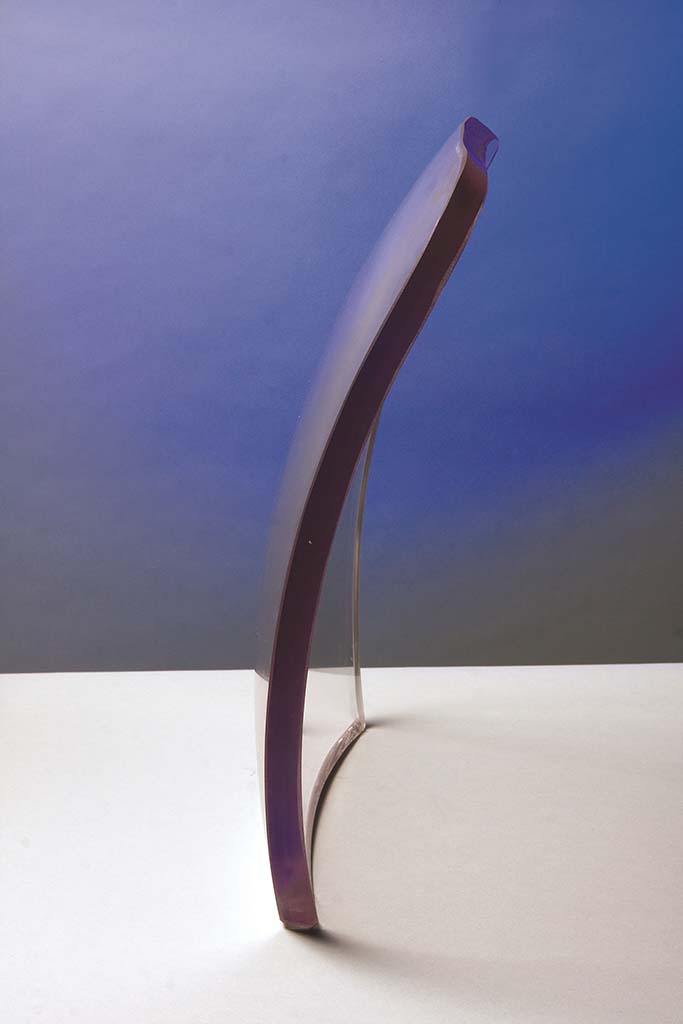
At the same time, Behm says there is a focus on processes to make curved glass or thin film substrates—especially relevant for business aircraft, which tend to use curved windows. “We can produce curved devices on glass now, but we envision plastics being feasible longer-term,” he says.
The OEM is also building upon its electronically dimmable window technology, which it initially launched in 2005-06 for application on the Boeing 787. Gentex’s more recent development is its “Gen 3” product for the Airbus A350 and Boeing 777X, which, according to Behm, represents an advancement over the older product—designated “Gen 2”—used on the 787. “That was slower [to dim]and not as dark,” he explains.
Gen 3 works by blocking light through absorption of the visible spectrum, using proprietary Gentex electrochromic technology. For comparison, Behm says Gen 3 blocks 99.999% of visible light, while Gen 2 blockage is 99.99%. For Gen 3, transition from totally dark to fully clear, or vice-versa, takes half as long as with Gen 2. “The passengers have individual control, and the cabin crew can also control the windows at the flight attendant panel if they wish to create a desired cabin light level,” Behm points out. The individual controllers, he adds, are extremely light, at approximately 150 grams (5.3 oz.).
“There is ongoing effort to continue evaluating both ultra-thin glass and plastic substrates for use in manufacturing our switchable tint devices. On film, the devices could be laminated to ultra-thin glass for reduced weight and longer durability,” explains Behm. “The lighter the weight of the material, the more sustainability, due to less fuel burned.”
Regarding another possible trend, Behm cites some interest in opacity, which uses liquid-crystal (LC) systems that scatter, rather than block, light. Specifically, they work by physically moving crystalline materials with voltage to scatter light.
“LC systems have not been installed on passenger aircraft other than maybe a few VVIP niche applications,” he says. “As with any system installed on an aircraft, they will need to be certified to meet the conditions for flight safety, flammability, temperature ranges, etc.”
Currently, Behm says opacity-based cabin windows are viewed as a competing technology or alternative to current systems. “The market should be nearly identical for long-haul airliners and business jets,” he says.
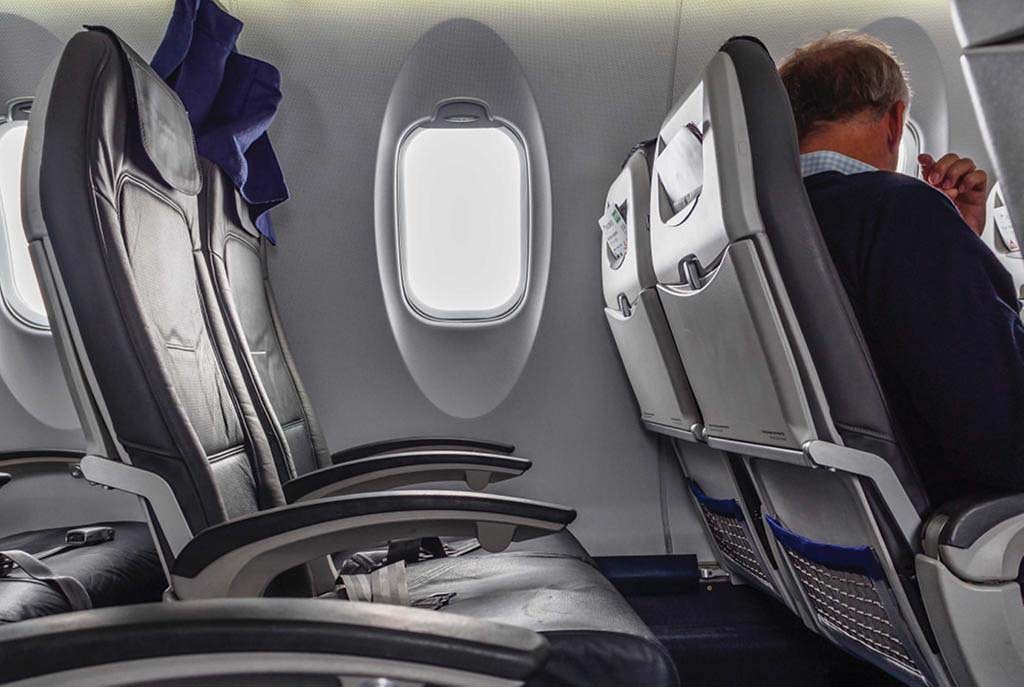
Scott Huth, general manager for aerospace at glass manufacturer Saint-Gobain, reports that the company is developing new cabin windows “with improved comfort capabilities” designed to reduce noise and heat in the aircraft cabin as well as new hard-coating material to protect the cabin windows material from scratches and chemical degradation. “They are tailor-made solutions developed and qualified for each specific customer’s requirements and environment,” he says.
At the same time, Huth stresses that acrylic-based materials remain the primary structural material for cabin windows. “Thickness, and thus weight reduction, can be obtained by a better integration and management of interfaces with the airframe OEM, to define the best thickness and deflection compromise,” Huth says. “Right now, there is no new game-changing material for cabin windows.”
Weight and thickness reduction are being achieved at Saint-Gobain through the use of “more generally chemically tempered glass” designed for aerospace applications, he says, which affords higher mechanical resistance and optimized weight. “Specifically, that uses polymethyl methacrylate, a stretched organic material,” Huth adds. “Examples include Saint-Gobain’s Solidion and Ionalex mineral glasses, produced in-house.”
He notes that “an increased utilization of laminate designs that balance the structural requirements, visibility, exterior impact resistance and aircraft weight” also continue to be pursued. However, he says laminated cabin window design is more relevant with respect to aircraft design architecture, interfaces and maintenance philosophy. “It won’t change cabin window behavior toward abrasion, which affects the external face of the cabin window,” he notes.
Brent Wright, global director of transparencies for aerospace products at PPG, says that stretched acrylic, “a known reliable material, well-suited for the cabin window application,” is the basic technology in service today on thousands of aircraft. However, within the past five years, PPG “has brought about innovations highly applicable to the cabin window space,” he says.
“Among them is Opticor, an advanced transparency material incorporating a new transparent polymer, offering a combination of high environmental resistance and optical clarity,” Wright explains. “The material is well-suited for cabin window applications, as well as wingtip glazings/lenses and rotorcraft fuselage windows. It is now flying on several models of business jets and one civil helicopter now in development.”
Opticor also offers some advantages over acrylic, Wright says, including slightly lighter weight and superior abrasion and chemical resistance, making it less susceptible to hazing and crazing over time. “Already in service for several years on certain business jets, the performance of Opticor to date is encouraging,” he reports.
Wright also says Opticor may be a life-extender for cabin windows. “Today’s stretched acrylic cabin windows can last 5-10 years in service, depending on operating conditions and coatings,” he says. “Because of its environmental durability, Opticor may offer a longer service life for cabin windows, but the jury is still out. That said, Opticor is already exhibiting superior service life in wingtip glazing applications.”
Another example Wright cites is Solaron Blue Protection UV+ Blocking window technology, which was introduced in response to increased concerns from the aeromedical community about the risks of cancer and eye damage associated with long-term exposure to harmful ultraviolet (UV) and high-energy visible blue rays, which are more prevalent at high altitudes.
“PPG aircraft windows incorporating Solaron offer increased crew and cabin protection by blocking the harmful rays,” Wright says. He adds that Solaron technically offers strong protection from 0 to around 430 nanometers, a harmful part of the light spectrum with respect to the threat of skin cancer and macular degeneration.
Wright says Solaron is typically used in dual-pane, laminated cabin windows as opposed to two-pane air gap windows. However, he says PPG is evaluating the possibility of augmenting Opticor with Solaron technology.
“We initially targeted flight deck windows with the Solaron technology, aiming for aircrew protection. But we have now seen that technology migrate to cabin windows in one business jet application,” he reports. “Along with passenger benefits, Solaron offers a protective benefit to the fabrics and materials in the cabin interior.”
There is, of course, the obvious question of what, if any, impact larger cabin windows will have on evolving window technology. That is more appropriate for the airframe design engineers rather than those in the transparencies industry, according to Wright.
“In sideward cabin-facing positions, the primary structural design driver is cabin pressurization as opposed to the dynamic threats we manage at the front of the airplane, such as potential high-speed bird-strike events,” he says. “Consequently, the thickness and attachment requirements associated with cabin windows are less challenging. Still, similar fail-safe requirements apply to both flight deck and cabin windows.”
Along with the technical innovations, cabin windows are being manufactured in a more sustainable way, with greater attention to recycling and disposability.
“PPG and other companies are obviously concerned with sustainability, now more than ever,” Wright says. “Aircraft design, safety and performance constraints are a challenge for sustainability. But PPG has been able to improve manufacturing sustainability through more efficient manufacturing processes and less energy-intensive equipment, such as, for example, more modern and efficient industrial ovens. On the material side, PPG has made great strides in chemistry, removing chrome from our transparency sealants and epoxy structural primers.”