Microbial Mitigation Matters More As Fleets Remain Idle

With much of the global commercial airliner fleet idled due to the COVID-19 pandemic, microbial contamination of fuel tanks has become a growing concern. The build up of harmful microorganisms can corrode aluminum and steel surfaces as well as break down the rubber system components specific to the fuel tanks.
It is not just a problem for aircraft sitting in desert storage for weeks or months. Research by Lufthansa Technik focusing on low-utilization aircraft found that fuel tank contamination is just as risky for aircraft still flying but at low utilization rates, says Ralf Riemann, Lufthansa Technik project leader for fuel tank inspections. “In general, aircraft with low flight cycles are very susceptible to fuel tank contamination and the resulting damage. Long ground times, especially in combination with warm to hot ambient conditions facilitate the formation of microbials and biofilm,” he says.
Riemann adds that once an aircraft fuel tank has been infected, a follow-up spread of the microbial load is much more probable, based on Lufthansa Technik’s experience. “Long-term storage requires closely monitoring the fuel system to prevent the initial formation and growth of microbial life.” He stresses that if an aircraft is “frequently flying with regular fueling,” the risk is comparatively low.
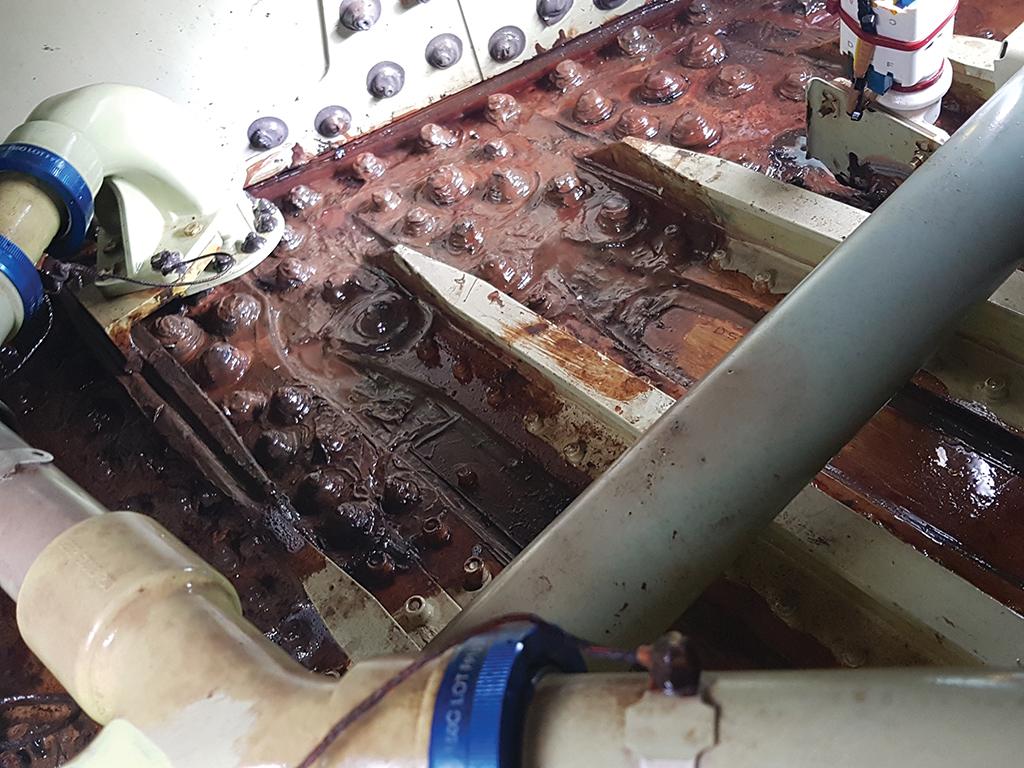
However, if an aircraft sits for more than a month, the fuel should be tested with a microbial test kit, suggests Art Smith, AAR Corp.’s chief quality officer. Neglecting to perform recommended inspection procedures will increase the likelihood of microorganisms forming. As an example, he points out that the fuel tanks of an aircraft in storage should be sumped—drained of the water and contaminants that collect at the low point of the fuel tank—and inspected for water and contaminates damage. “Aviation fuel tends to absorb moisture from the atmosphere, so aircraft with more usage of fuel are less susceptible,” he says. “If the fuel is constantly used, there is no time for this issue to occur.”
Microbial buildup in the fuel tanks can also lead to collateral damage, clogging engine fuel filters, for example. As Anthony Laude, senior systems engineering technical leader at GE Aviation explains, microbial contaminants themselves are usually captured by the engine fuel filter. The filter, which he says is a consumable and easily replaced as a line maintenance item, incorporates a monitoring pressure system that issues an alert to the pilot if it becomes clogged. Should that happen, the filter would go into a bypass mode, and the microbial contaminants from the fuel tanks might reach and block the fuel system tubes and passages. “The blockage would have to be addressed by sending those affected components to a maintenance shop,” Laude notes.
The best defense against fuel tank microbial buildup is to comply with the recommendations in the aircraft OEM manuals, which include proactive treatment procedures, says Laude. “The aircraft fuel tank inspection is up to the operators and triggered by the level of contamination detected by fuel sample testing,” he notes. “Operators are expected to regularly test their fuel tanks for microbial growth.”
To prevent such growth, Laude mentions two chemical biocides that GE Aviation has approved, but one of the products, Kathon FP 1.5, from Dupont, was removed from the OEMs’ approved list of fuel additives following repetitive field issues due to misapplications. In fact, a Kathon FP 1.5 misapplication was cited by the UK Air Accident Investigative Branch as the cause of a “serious incident” that nearly resulted in the loss of an Airbus A320 in the UK. The biocide was discontinued for aviation use in March of this year.
Biobor JF, manufactured by Hammonds Fuel Additives Inc., is now the only available GE-approved product, but it is currently not approved for use in the European Union. However, that may change shortly.
“About 15 EU member states have allowed temporary use of Biobor JF in order to help European operators cope with their high volume of parked aircraft,” says Laude. “The industry is working on future biocides that will have to be assessed by GE and other aircraft, engine and APU OEMs, and approved by local governmental authorities as well.”
Christian Siry, head of Lufthansa Technik’s Central Materials Technologies unit in Germany, says problems with microbial buildup can occur when fuel tanks constructed of aluminum alloys are filled with jet fuel. Problems from micro-bial contamination do not arise from “individual planktonic microbes” in the fuel itself but from the biofilm growing at the interface of condensation water and fuel and from biofilm at the bottom of the tank, he says.
“Corrosion occurs mainly on the bottom of the fuel tank below the growing biofilm. If not detected and removed at an early phase, it can lead to large defective zones,” Siry explains. “Fuel filter clogging may take place with potential impact on fuel flow integrity, and the fuel quantity indication system may show signs of fuel quantity fluctuation.”
Siry also points out that in some cases there are signs of microbial infestation in other fuel system components, such as high-precision, fuel-wetted flight control units. “A closer look into the fuel system with modern detection techniques has revealed—and suggests—that more interference from microbial loads may occur than previously thought,” he says.
Lufthansa Technik’s research also shows a strong correlation between the risk of corrosion and microbiology layers in the contaminated area. The reason, he explains, is the formation of well-adhering biofilm zones. “The survival capabilities of biofilms are remarkable, since water and humidity protect them against any toxic and biocidal attacks, enabling them to attack the tank wall through acidic micro-channels formed within the biofilm,” says Siry. “The mixing of biocides with the fuel is not resolving the problem once the biofilm formation has been established.”
Siry adds that Lufthansa Technik and the University of Hamburg have started a research project to develop a more accurate method for early detection of all microbiological contamination. It also allows for classifying the contamination as critical or not critical.
“The employment of adjusted DNA technology considers the whole environment of the airplane operation—rather than fuel testing only—as an indirect indication of the fuel system microbial contamination problem,” he says. “Thus, a comprehensive fuel filter analysis and other fuel system components have already supported early warning indications,” he says. The next part of the research is developing an “improved cleaning approach to ensure the reliable removal of the biofilm contamination.”