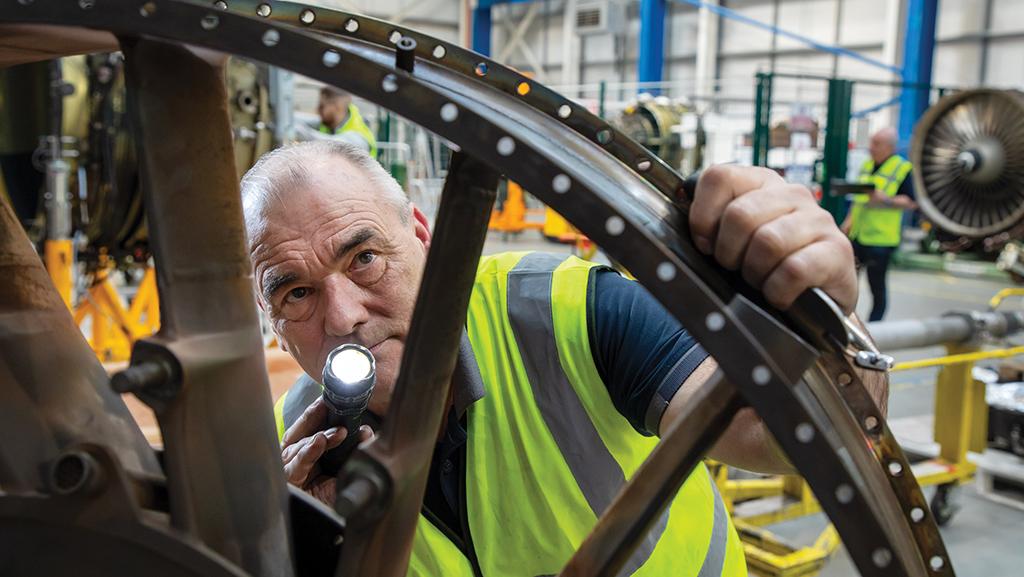
A high number of lease extensions is reducing the supply of aircraft and engines that could be torn down for used serviceable material.
European carriers recorded a 60.6% increase in passenger traffic in January compared with the same month in 2022. Continual growth in traffic numbers throughout the spring and summer brought average European passenger load factors to 87.7% by June.
However, in conjunction with delays in new aircraft production and fewer aircraft teardowns, this growth is increasing pressure within the components and parts supply chain. Operators are retaining older aircraft to address capacity deficits.
“The used serviceable material market is on fire in terms of the ability to sell material,” says Lee Carey, vice president for asset management at EirTrade Aviation. “The acquisition of aircraft and engines for disassembly is becoming more difficult due to delays in the delivery of new aircraft.”
According to Jonathan Berger, managing director at Alton Aviation Consultancy, new global aircraft production halved to just 600 new deliveries in 2020 before increasing to 700 in 2022. The number of aircraft retirements at this time remained relatively low as most of the grounded fleet was placed in long-term storage.
“The lead time for necessary parts and to replenish stock inventory is now typically longer,” Berger says. “The component repair shops are flush with work, and there is a shortage of [used serviceable material]. Sometimes airlines and MROs must now buy new because there are no used alternatives available. This is significantly increasing airline cost.”
High demand for important engine and airframe parts and components means some are out of stock completely from the OEMs, and lead times remain long. Additionally, manufacturers of new parts must decide which components to make and where to allocate them.
“The OEM must identify the parts needed for new-build aircraft and those needed for spares inventory,” Berger says. “In general, the OEM parts supply situation is improving, and it is a lot better than a year ago. It is working itself out. However, engines remain the most troublesome area. Supply chain issues and a lack of spare parts, [as well as] manpower, are affecting engine shop visit turnaround times for both new-generation and legacy engine types.”
There is little to no used serviceable material (USM) available for new-generation engines, as it is not economical to tear down the expensive assets at an early age. The issue is compounded because new Pratt & Whitney geared turbofan and CFM International Leap engines have not reached maturity, having less time on wing in comparison with legacy alternatives.
Legacy assets are also suffering, as high demand for overhauled parts means many repair specialists cannot keep pace. The long wait for some parts and components means many older-generation assets remain in an unserviceable condition.
According to the Aviation Week Network’s Commercial Fleet & MRO Forecast, the European fleet consists of 7,700 active aircraft, 67% of which are narrowbodies, 17% widebodies and the remainder regional jets and turboprops. Most of these aircraft are mid-generation types such as the Boeing 737NG and Airbus A320neo families of aircraft equipped with CFM56 and Pratt & Whitney V2500 engines.
Aviation Week’s forecast projects that 546 CFM56-7Bs, 434 CFM56-5Bs and 364 V2500s are scheduled to visit a shop in 2024. New-generation Leap 1A and 1B shop visits are forecast to total 1,958, and PW1100G shop visits 1,494. Alton Aviation Consultancy forecasts that 43% fewer aircraft will be retired in 2023 compared with 2019, resulting in less used material for operators and MROs. However, Aviation Week forecasts about 15% more aircraft retirements in 2024 compared with 2019.
“The high number of lease extensions is lowering the supply of aircraft and engines made available,” EirTrade Aviation’s Carey says. “This reduction in supply leads to a natural increase in terms of price, which naturally rolls on to the USM market. From an availability standpoint, there was once a surplus of material because of the lack of demand during the pandemic. However, it is quite the opposite in the current market.”
Carey says continuing consumption of components caused by high passenger traffic and high aircraft utilization rates is drying up material surpluses. Life-limited parts (LLP) for midlife narrowbodies—high-pressure turbine blades and Stage 1 low-pressure turbine vanes—are in “remarkably low supply,” he says. “It was even difficult to source this material before the pandemic. It is next to impossible to get them now,” he adds.
Turning to the OEMs for high-value parts and components such as LLPs means that asset owners must be committed to that product for a longer period to extract the maximum return from the investment.
“While lead times at the repair shops have improved somewhat, it is still a major delay which we need to plan for on each project,” Carey says. “To allow EirTrade to improve efficiencies, we are very focused on acquiring assets which can be disassembled at our own aircraft and engine disassembly facilities in Ireland. This allows us to have more control over any given project and improve the [return on invested capital] by improving these timelines.”
EirTrade recently opened an engine disassembly facility in Dublin to help minimize engine teardown time and leverage control across its supply chain. By bringing CFM56-3/-5A/-5B/ and -7B engine disassembly in-house, Carey says EirTrade has better flexibility around its own acquisitions and customer teardowns.
“Secondly, there is a shortage of engine disassembly facilities in Europe,” he notes. “Lots of people were reliant on larger MROs in Europe that have a primary focus on lucrative shop visit agreements. As they get busier, they do not necessarily want to disassemble engines, which we believe has created a gap in the market.”
Engines earmarked for teardown in 2023 have completed a greater number of engine flight cycles than forecast. Therefore, assets that would normally have about 5,000 engine flight cycles remaining before teardown now have significantly fewer. The demand for surplus engines with meaningful remaining green time has increased dramatically as a result.
“USM companies such as EirTrade want quick turnaround times from their repair vendors to facilitate material being brought to the market quicker, which helps us serve the needs of our clients better and improve the financial performance of each project,” Carey says. “We are now more focused than ever on utilizing specific repair shops which can offer these efficient turnaround times and building very close relationships with these suppliers.”
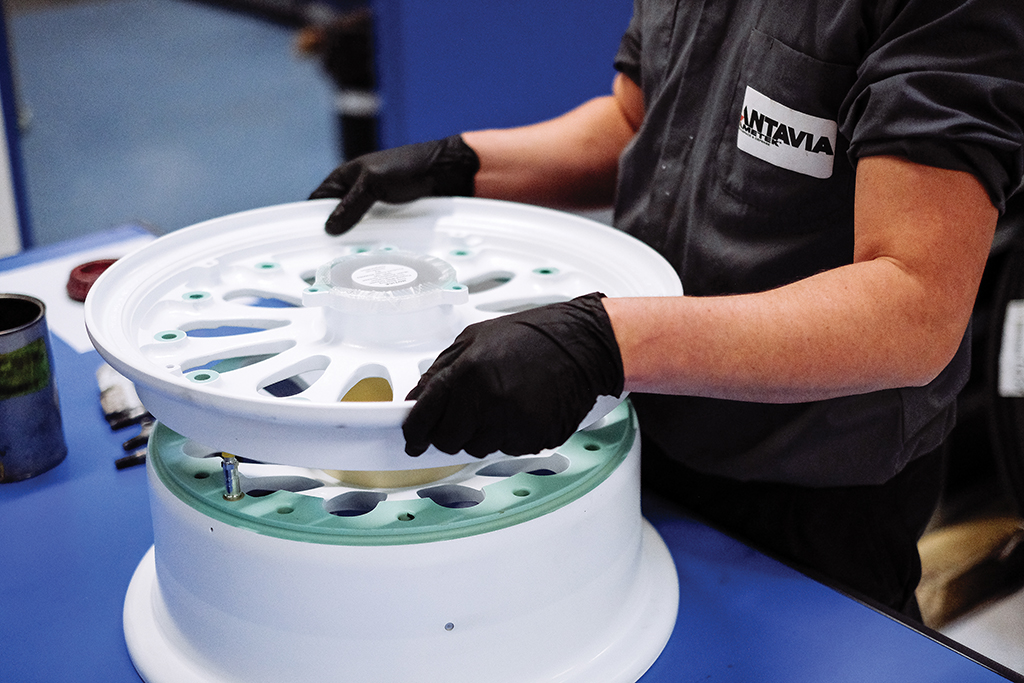
Ametek MRO has six main product lines: actuation, thermal management, landing gear and brakes, avionics, safety equipment and power generation. “Wheel and brake components remain in high demand, and the supply situation has been challenging throughout 2022,” says Ismael Fadili, Ametek’s vice president for sales for Europe. “Sourcing tires and brake heat sinks has been difficult overall, [but] the situation is now improving. The procurement of printed circuit boards and other small electronic parts has been difficult.”
Ametek publishes monthly stock forecasts for some of its suppliers, giving end users an idea of delivery and schedule. In terms of output, Ametek is now ahead of its yearly forecast in many areas.
“Finding skilled technicians is a challenge. On the technical side, it is complicated to find the right people in the right location,” Fadili says. “As the supply chain improves, the demand for labor is increasing, so our main focus over the next months will be to find technicians.”
Fadili says it can take 6-12 months to train a technician, depending on their focus area. Wheel disassembly, cleaning and reassembly are comparatively simple, yet the nondestructive testing element means it can take up six months before a wheel technician is fully trained. Avionics components take longer to learn, and Fadili says it can take up to 12 months before a technician is at a good standard. “If we are not finding the right technicians today, then this could mean there is an issue in 12 months’ time,” he adds.
Many more unscheduled landing gear removals have been conducted over the past six months, and the trend is expected to continue due to increased utilization levels of passenger and freighter fleets.
Sourcing single supplier parts can be problematic because of the lack of an alternative, and the number of parts manufacturer approval (PMA) parts and designated engineering representative (DER) repairs is growing steadily as a result.
“In Europe, there is some reluctance to use PMA for engine and safety components. PMA usage is most common in the cabin,” Fadili says. “Today, PMA parts can be more dependable than OEM counterparts, yet there is little discussion about that.”
Ametek is recoring heat exchangers and can also complete DER repairs on electronic solenoids for cockpit door tracks. A new solenoid will cost thousands of euros, while a DER repair can cost hundreds. “It is difficult for some OEMs to stock all the components needed for DER repairs. It then makes more sense for OEMs to sell an entire new line replaceable unit than parts,” Fadili says.
Although delays are improving compared with 2022, European MROs expect to be even busier in the next couple of years as recovery in the region continues, which could lead to other challenges for OEMs and repair vendors in the future.