Opinion: Aviation Must Align On Parts Traceability Vision
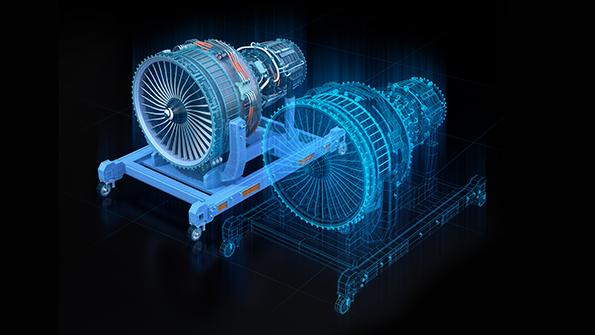
Back-to-birth traceability of aircraft parts is an issue that numerous industry organizations have been facing for a long time. That is because the transfer of aircraft parts between industry stakeholders is inherently linked to regulations and commercial contract provisions around the maintenance history of those parts. However, the lack of a common industry approach to traceability creates unnecessary bureaucracy and interminable negotiations between the trading partners, all conducive to frustration, time wastage and significant loss of asset value.
Digitalization allows us to maintain parts traceability far more efficiently than paper-based processes. Interestingly, the pandemic has dramatically reduced opportunities for face-to-face exchanges but greatly accelerated the drive toward digitalization and development of innovative data-exchange concepts. Equally important is the recognition and acceptance by the International Civil Aviation Organization and key aviation safety regulators of digital documentation for aircraft parts.
Now it is time to take the next step and fully enable the industry to track and trace an aircraft and its parts around the world and throughout time using digital technology.
Digital cradle-to-grave parts traceability will help to address multiple situations, such as aircraft and parts subjected to sanctions, regulatory and commercial requirements, internal company policies and procedures and other cases. Beyond airworthiness assessment, traceability can assist in the financial evaluation of the asset.
An industry standard is essential so that requirements can be set to trace the history of aircraft parts properly from their production to delivery and throughout their operational and repair activities.
In the absence of such a standard, an understanding of the differences among various regulatory and commercial needs—as well as the ability to exchange data and information efficiently among parties—would be a significant step. No such common understanding of traceability requirements exists among all the industry stakeholders trading aircraft parts. This issue affects a sector of the industry that represents approximately two-thirds of the annual $90 billion MRO market.
At least two aspects must be addressed to facilitate parts traceability. The first is an industry agreement that allows for the creation of a “digital twin” of the physical part—basically, a digital folder that contains the history of the part and its events, movements and transactions. The current operator (and owner, if different) has full access to the aircraft part and should have access to and control of its digital twin, including the ability to add any additional information generated about the part during operation.
The challenge will be for the industry to agree on the type and format of data that needs to be traced from the part’s production to the end of the part’s useful life—a task like the development of an e-ticketing standard that facilitates passenger traceability across the airline industry. Blockchain is a technology that can be employed to ensure data immutability, a critical property to ensure the need for trust among participating entities. Cloud technology with proper governance rules can allow access to data as needed.
The second challenge arises from the inherent need to link the physical part with its digital twin through auto-ID technology, such as machine-read laser etching, QR code or RFID tag. The uniqueness of a digital identity for the part itself and for the individuals and the entities linked to the part must be addressed as critical elements enabling data exchanges among systems.
The infusion of new digital technologies using commonsense standards will lead to a solution that addresses the operational, supply chain and cost challenges associated with back-to-birth parts traceability. As the so-called “digital natives” enter the aviation workforce in greater numbers and the industry resets after COVID-19, the time has come to align on a shared vision for the most efficient use of digitalization to support this vital requirement.
Chris Markou is the head of operational cost management at the International Air Transport Association.