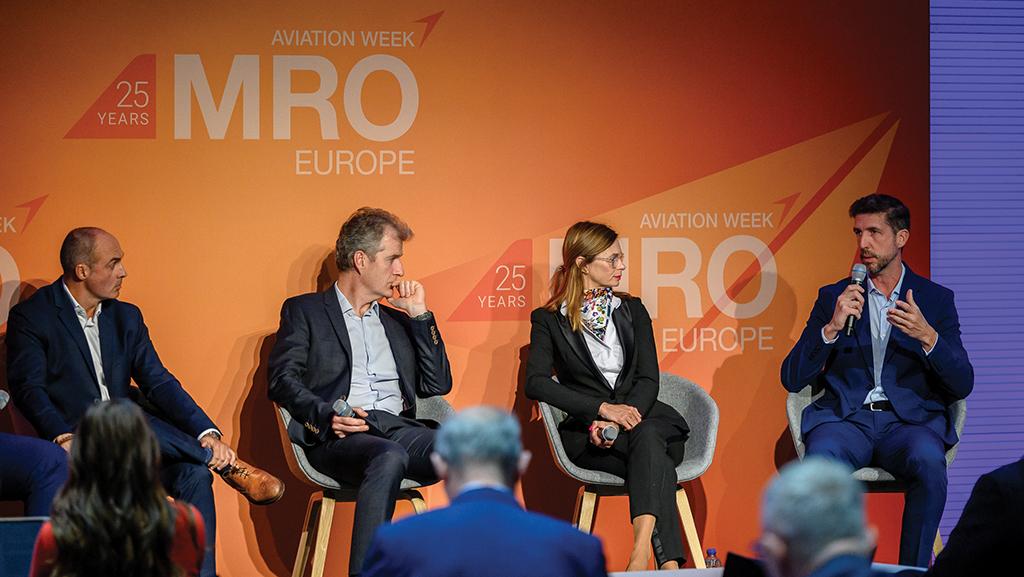
Panelists at MRO Europe included (from left) Oscar Perez, managing director of Globalia Maintenance; Benjamin Moreau, senior vice president for strategy and business development at AFI KLM E&M; Maria Guilarte Polanco, head of transformation at Iberia Maintenance; and Alejandro Ceballos Gallego, director for supply chain, engine assets and aircraft transitions at Aer Lingus.
At Aviation Week’s MRO Europe in Amsterdam in October, aftermarket executives from around Europe discussed what is working well for them and the hurdles their businesses are facing.
Close Quarters
Demand ramp-ups in airframe, engine and component MRO will challenge Europe’s capacity-constrained aftermarket as MRO providers look at ways to improve readiness. In airframe maintenance, where airlines see insufficient slot availability particularly in base maintenance, MRO providers have tried to add physical space to address constraints. Oscar Perez, managing director at Spanish airframe MRO company Globalia Maintenance, says it plans to add capacity outside of its main base in Palma with a new hangar in Madrid. Scheduled for the first quarter of 2024, the new hangar will have three widebody positions. “Adding hangar space is one way—albeit an expensive way—of adding more capacity,” he says. “The industry needs to focus a lot more on squeezing all of the resources we have available to drive operational efficiency, from supply chain to manpower. We need to make sure we can do more with less.”
In Europe’s engine segment, Maria Guilarte Polanco, head of transformation MRO at Iberia Maintenance, says the company is seeing smaller workscopes, especially for engines. Able to retain most of its staff through the pandemic, Iberia Maintenance was well-positioned to meet returning demand and is focusing on absorbing future demand increases, Polanco says. “When we negotiate our slots for the next year, we are working more closely with customers to understand their needs and have tried to adopt flexibility in our operations to do this,” she says. Polanco cites these operational changes as driving continuous improvement initiatives, expanding capacity at its facilities, acquiring new tooling and investing in new technologies.
Iberia has also prioritized training existing staff, given its specialization in narrowbody engines, and it is anticipating future life-limited parts replacements on CFM56-7B and IAE V2500 engines along with scheduled inspections for around 3,000 Pratt & Whitney geared turbofan engines mandated through 2026.
Another developing dynamic is the greater localization of repairs. “We see the increasing attractiveness of nearshoring maintenance not just in airframes but also in engines and components—airlines are looking for that,” says Benjamin Moreau, senior vice president for strategy and business development at AFI KLM E&M. “Of course there is an economic dimension to this, but also a sustainability one,” says Moreau, who sees Europe and some Asia-Pacific countries as leaders in sustainability driving the nearshoring of MRO. “We are also adjusting our geographical footprint worldwide for engines and components to be closer to operators.” As AFI KLM E&M prepares for new-generation aircraft types, it is also maintaining a strong focus on current-generation models, which “are still a major chunk of the MRO market, so we need to maintain capability and capacity in those domains,” he says.
Slow Turnarounds
Turnaround time (TAT) in the component repair segment has improved to some degree this year but still lags far behind 2019 levels. Kim Ashmun, president of StandardAero’s components and accessories division, cites workforce as a key obstacle. She says that although the company retained staff during the pandemic, helping its TAT, other labor-related factors have remained problematic. “People who weren’t ready to retire but were in that retirement time frame made the decision to retire, which meant a loss of expertise and talent,” she says. Now the U.S.-based company is partnering with OEMs and its supplier base to further reduce TAT, Ashmun says.
Frank Haberkamp, vice president for repair services at MTU Maintenance, says labor has also impacted the company, with younger workers moving around the job market after a few years of employment. Machinery and tooling availability is also contributing to TAT lags. Haberkamp says approvals to buy parts for certain types of inspections can come through in little more than one week, yet the delivery of some parts or tools can take up to two years. Martin Mintel, components and spares division head at Czech Airlines Technics, says that since the pandemic, the MRO provider has looked to diversify its supply chain to avoid lengthy TAT.
Matthew Davies, general manager at AAR subsidiary Airinmar—which helps manage component repairs for some 25 airlines—says the company’s standard for a “good” TAT has not changed since pre-pandemic days. “Our target is 10 days for avionics and 15 days for everything else,” he says. Drawing on a customer case study in 2018-19, he says its average workshop TAT was around 29 days. “Fast-forward to 2023, and that same customer now has a workshop TAT of around 54 days,” he says. “If I cut out all of the buyer-furnished equipment suppliers from that analysis, it drops down to 34 days—so not as big an increase as some might think but still way off that 10-15 day target.”
Looking Outward
Sluggish growth in Europe’s aftermarket and global geopolitical challenges are not stopping some European MROs from growing across the continent or eyeing new opportunities farther afield. Poland-based Avia Prime is still feeling the inflationary impact of the war in neighboring Ukraine, which has ratcheted up costs for labor, parts and energy. CEO Piotr Kaczor cited the Asia-Pacific region and the Americas as areas for possible expansion.
Revima Group, a France-based repair specialist handling auxiliary power units, landing gears and engine components, has expanded overseas in recent years, notably opening a landing gear repair facility in Chonburi, Thailand, in 2020. President and CEO Olivier Legrand says the business’ strong performance—with three times more work volume this year compared with 2022—has led the company to consider markets such as India, long anticipated to develop into one of the largest MRO locations in the world. The hundreds of new Boeing and Airbus aircraft orders placed by Air India and IndiGo have further buoyed this trend. However, Legrand is cautious about expanding into India for component repairs, given the country’s current lack of maturity and the less immediate need for MRO on new-generation aircraft landing gear.
Lufthansa Technik, which previously considered a presence in India, is also watching the country’s MRO development. “The numbers are pointing in the right direction, and the government is taking steps in the right direction, but there are still huge challenges,” says Sven Taubert, head of corporate strategy and market analytics. “If you prioritize on a global scale, India is not currently at No. 1 for us. But will that be the case next year or the year after? Maybe that’s changing a lot because India is developing very fast.” Taubert sees a joint-venture approach as the best option for foreign companies seeking to set up shop in India.