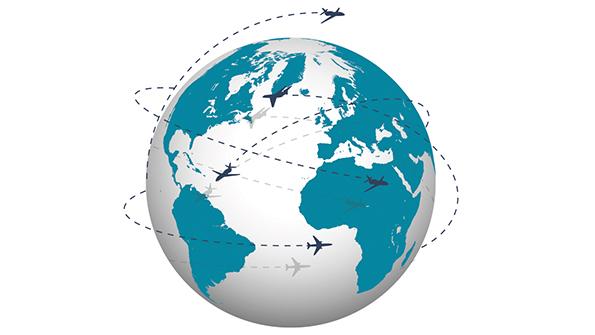
Having just flown 32,929 mi. in the past 24 days for work, I’ve talked with lots of people from airlines, MROs, suppliers and OEMs—from most continents of the world.
The one topic that came up most frequently in these conversations? Supply chain problems.
While there are pockets of improvement, most in this industry anticipate that supply chain woes will not improve much this year.
Soren Stark, Lufthansa Technik CEO, agrees. “I do not expect that the situation [the performance of suppliers] will ease by the end of the year. I think this is something structural, which will continue at least into the next year,” he said on March 7, during the company’s annual results briefing.
While no one had a playbook of best practices for surviving a pandemic, several executives, including Stark, admit that keeping skilled technicians employed would have been a better choice to help with the eventual recovery, despite the drop-off in demand. But the world was in survival mode, and this is a view using 20/20 hindsight.
Around the world, there are a lot of engines in WIP (work-in-progress), which was not the case pre-pandemic. The problem affects both new and used parts—the latter often have to be repaired once shops find the unserviceable parts. And repairs can take much longer than they did pre-pandemic, too.
What is the industry doing to mitigate these problems?
Repair Development Companies are investing more in repairs—from engines and APUs to nacelles. While repair development is not a new concept, “whereas customers used to buy a new part or get an exchange,” due to a shortage of parts now, “we’re repairing things that maybe in the past were considered beyond economic repair,” says Olivier Legrand, president of Revima.
Parts Stocking MROs are buying more spare parts, especially to support aircraft on ground.
Technology Aeroman, for example, is trying to use predictive technology to pre-stock consumables and rotables it will need before a heavy check.
In-house Capabilities Aftermarket companies are adding capabilities in-house that they used to outsource. Etihad Airways Engineering, for example, is expanding its footprint and capabilities to grow its business and tighten turnaround times by controlling more of the parts and processes in-house.
Teardowns Several MRO providers are thinking about buying aircraft to dismantle for parts. Related to this, used serviceable material consumption is increasing as new-part prices escalate.
3D Printing Magnetic MRO printed a long-lead-time item: a bracket for a tray table.
Communication Its importance cannot be overstated—talk with suppliers to understand the problems and work cooperatively toward solutions.
When talking about materials, “this is not something you can easily switch from A to B when we are talking about repair services,” Stark says. “Lufthansa Technik can ease the pain of the supplier if it is willing to let us do a part of it . . . and provides IP access,” but “that’s unfortunately the exception rather than the rule.”