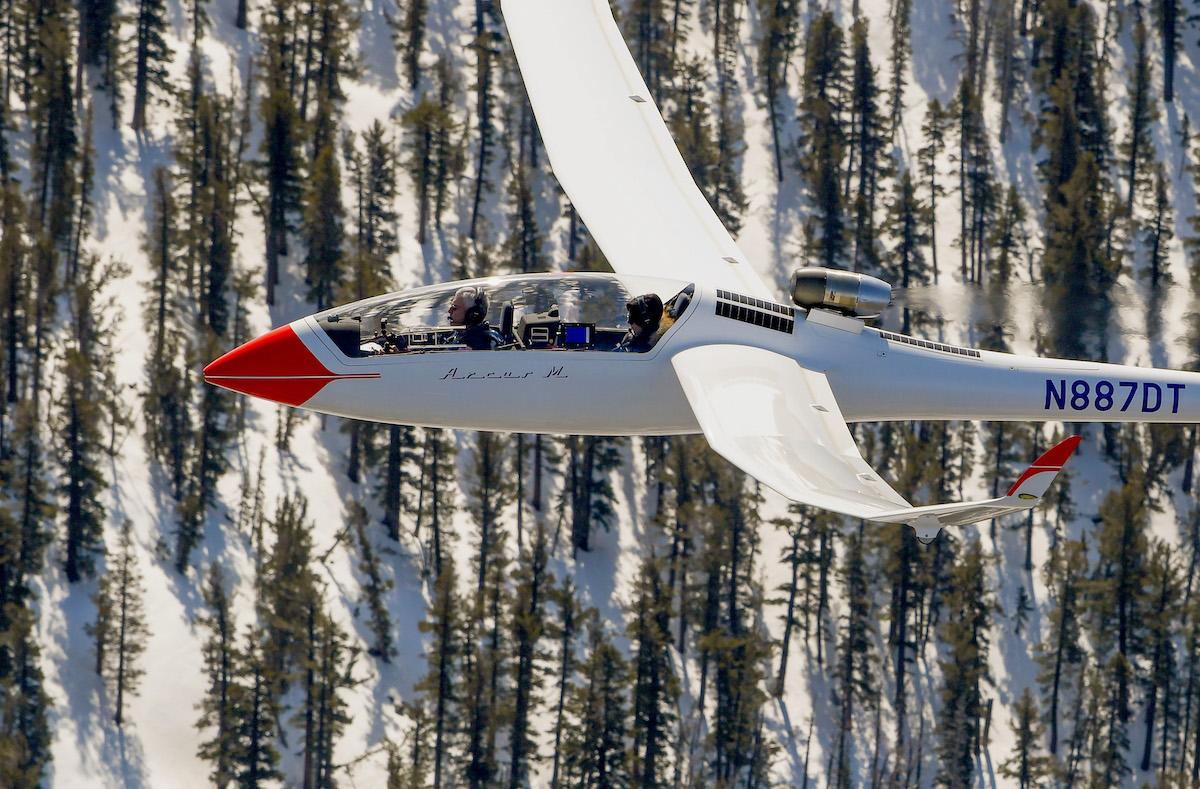
FARNBOROUGH—Airbus UpNext, the aircraft maker’s technology innovation arm, plans to flight test a hydrogen-burning engine at altitude on a powered glider early next year as part of research into contrail formation.
The radiation effect of persistent contrails makes the greatest contribution to the non-CO2 climate effects of aviation, yet the impact on contrails by using hydrogen—either directly combusted in an engine or in fuel cells—remains one of the biggest unknowns facing the aerospace industry as it evaluates alternatives to jet fuel.
As well as measuring hydrogen’s impact on contrails, the project—dubbed Blue Condor—will provide Airbus with early experience of direct hydrogen combustion in a turbine engine as well as a greater understanding of the operational and safety factors associated with using the fuel. The initiative comes almost two years after Airbus signaled its long-term goal of switching to hydrogen in pursuit of sustainable aviation growth and the development of a next-generation carbon neutral airliner for entry into service by 2035.
Airbus and CFM also plan to flight test a GE Passport engine modified for direct combustion of hydrogen fuel. The tests, scheduled for around 2026, form part of the wider CFM RISE engine technology development effort and are intended to pave the way for entry into service of the first of several generations of planned Airbus zero-emission aircraft by 2035.
But Blue Condor will come a lot sooner. “For the first time ever, Airbus will be flying a hydrogen-burning engine,” says Sandra Bour Schaeffer, head of the Airbus UpNext project. “We will also learn how to operate that engine—on a small scale certainly—and it will also help us to understand the impact of a hydrogen-burning engine on the environment,” she adds.
Working with the Airbus-sponsored Perlan 2 stratospheric glider project team, Airbus UpNext plans to evaluate the impact of hydrogen using a pair of Arcus-J aircraft—a version of the Schempp-Hirth Arcus M sailplane powered by a small retractable turbojet. “We are trying to get an understanding of contrail formation through the burning of hydrogen compared to kerosene,” Schaeffer says. “So one will fly with a hydrogen-fueled engine and the other with a kerosene engine.”
Although originally fitted with a PBS Aerospace TJ-100 turbojet, the test aircraft will be modified with a special hydrogen-burning version of a small engine developed by Germany-based Aero Design Works. The engine is a “very simplified version of a fully fledged kerosene engine and what would be a hydrogen combustion engine in the future—the importance is to concentrate on the formation of contrails and understand, and measure precisely, what is in them,” Schaeffer says. “We already know hydrogen combustion produces more than 2.5 times more water vapor than current jet engines, as well as a bit of nitrous oxide (NOx), but it does not produce any soot. So it is very important to understand the detailed composition.”
The experiment will be focused on comparing the contrails as they are generated simultaneously by the two sailplanes in the same air mass. “It is about comparisons between the two and the ability to derive models out of that,” Schaeffer says. Because the characteristics of contrails produced by Jet-A are better understood, Airbus plans to extrapolate from its observations and compare the data to the results from the hydrogen burning engine.
The contrails will be sampled by a suite of instruments developed by German aerospace center DLR for the Emission and Climate Impact of Alternative Fuel experiments (ECLIF) in the 2010s, which measured the exhaust from different types and blends of standard and alternative fuels. ECLIF also included cruise-altitude measurements of emissions using the instrumented DLR Falcon 20.
For Blue Condor, the instrument suite will be mounted on the Grob G520 Egrett, a single-seat, single-turboprop aircraft designed for high-altitude research and surveillance. It was also used by the Perlan project to tow the Perlan 2 glider to release altitude for its record-breaking flights over Argentina. The Egrett will simultaneously tow both Arcus aircraft to altitude before releasing them and repositioning behind the sailplanes to sample the contrails. This method will enable data collection of both contrails in the same air mass and altitude at very close timescales.
Perlan Project chief pilot Jim Payne says Airbus UpNext selected the sailplane research unit because “they were looking for an organization that was kind of lean and had a good track record and could pull it off. So, it’s been almost over a year and a half ago since they approached us and we’ve been doing a buildup to the test program ever since.”
To date this has included practice tests in Texas with the Egrett and an Arcus-J fitted with a smoke system. “We’ve subsequently gone to North Dakota and flown up to flight level (FL) 330 where we actually sampled real contrails. The contrail level is a little bit high for an unpressurized aircraft, so we set FL330 as a limit for unpressurized operations, and if you look at the weather of the United States, normally contrails don’t form that low except in the wintertime or the late spring in places like North Dakota,” Payne says.
A gaseous hydrogen system will feed the test engine, and tanks for the fuel will be installed in the two-seater sailplane’s rear cockpit. “We have an extensive instrumentation system to measure temperatures and pressures, and we’ve done extensive work with respect to leaks,” Payne says.
“Of course we will be a little bit fuel limited, so the plan is to tow at about 18,000 ft. we’ll start the engine and run it in idle until we get to release altitude. We will push the power up and we’ll do a reposition maneuver so the Egrett moves to the aft and commence our flight testing,” says Payne, who estimates that “we will get maybe 10 to 15 min. of full-power operation once we get off of tow.”
The sailplanes, which have a 50:1 glide ratio, will then recover to the test base at Grand Forks, North Dakota. “This airplane has plenty of performance for returning back to Grand Forks and if we misjudged the wind or something, there’s many airports we can land at,” he adds.
Initial handling qualities of the TJ-100-configured Blue Condor aircraft began in early July, with follow-on tests of the aircraft modified with the new engine later in the year. “But we won’t be ready to use hydrogen then until probably in later September, or maybe October. Then we’ll have the whole system and we’ll be able to do the first flight with hydrogen,” Payne says.
Initial flights with hydrogen will be at low altitude because “we won’t have the Egrett. So, for those flights will probably start the engine on the ground and tow to 10,000 ft. above MSL here at Minden, Nevada (the Perlan base) and then we will commence our initial tests, looking at the performance of both the engine and the fuel system.”
Once data acquisition is completed, the Blue Condor project will be over—but Airbus expects to make further, as yet undecided, use of the aircraft.
“I’m sure we’ll find other interesting ways to use and operate them,” Schaeffer says. “The teams already have a number of ideas. We have to do selection on that.”
“This is the philosophy of our innovation,” say Sabine Klauke, Airbus’s chief technical officer. “UpNext is always defining two-year projects, specific projects, in order to have quick turnover, quick findings, quick learnings. Blue Condor will be ending, but we will build on that and define the next steps.”