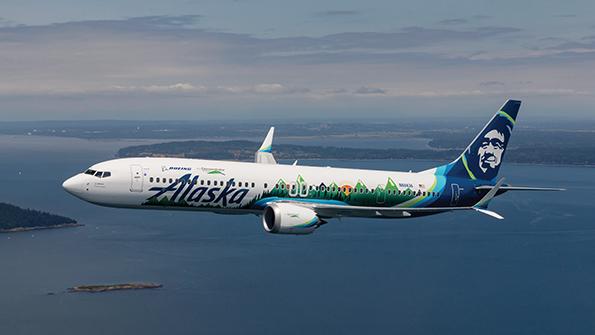
Almost a decade after the ecoDemonstrator program began, the Boeing initiative is gaining in importance, as the strategic development spotlight falls squarely on sustainability and the maturation of new technologies for its next new aircraft.
- Alaska Airlines 737-9 is eighth ecoDemonstrator
- Program has tested almost 200 technologies to date
The significance of the ecoDemonstrator, both as a technology testbed and as a tangible symbol of Boeing’s drive toward a reduced environmental impact, has been underscored by its continued annual funding even throughout the last two bleak years of the COVID-19 pandemic and the 737 MAX grounding.
“Investing in sustainability is investing in the future,” says Mike Sinnett, vice president and general manager of product development for Boeing Commercial Airplanes (BCA). “You have to do that. The pandemic has been an incredible time for all of us in the industry, and I’ve been proud of the company’s willingness to continue to invest in these things that matter. It might have been easy to just pull the plug and say we can’t afford that right now, but we can’t afford not to invest.”
Sinnett adds that, despite the unprecedented problems confronting Boeing amid the virtual collapse of the international air transport market, the team continued to make progress. “We ran an entire ecoDemonstrator program in 2020 with a 787-10 and our partner Etihad Airways. We made probably more progress in understanding noise generation, noise sources and ways to design to improve the noise footprint of an airplane than we’d ever made in such a short period of time.”
Now, as a new set of 20 discrete technologies continues to be evaluated on the latest aircraft to feature in the program—a 737-9 on loan from Alaska Airways—Sinnett says sustainability is emerging as an increasingly important design parameter for the next new aircraft.

“It is going to be a driving factor—potentially a competitive advantage—certainly a requirement of entry into the market,” he says. “And when we think about sustainability, we truly are thinking about the entire life cycle—we’re thinking about the production system [and] the materials used during the production of the airplane. We think about how the airplane is maintained and the materials used during maintenance.”
Sinnett says the role of the ecoDemonstrator series will therefore principally be to continue to evaluate near- and midterm technologies to support the broader push for sustainability rather than step-change, breakthrough innovations. Boeing hopes to test these advances, including future aircraft-level design and propulsion system concepts, on projects such as NASA’s sustainable flight demonstrator—a new single-aisle X-plane project. Boeing is proposing its transonic truss-braced wing concept for the X-plane, which is aimed at testing and maturing key airframe-focused technologies for introduction on future single-aisle airliners by 2035. The X-plane is expected to begin flight tests in late 2026.
In the current project, unlike earlier ecoDemonstrators that operated as testbeds for weeks or a handful of months, the Alaska 737-9 will be flying experiments through December. “It’s one of the longest test platforms that we’ve had,” says ecoDemonstrator Program Manager Rae Lutters. Some of the focus is on continued themes such as advanced avionics, reducing community noise and utilizing sustainable aviation fuels (SAF).
The program with Alaska, the first ecoDemonstrator to utilize the 737 MAX derivative, also marks a rebound in terms of the number of technologies under test. Until 2020, when the impact of the pandemic restricted the effort to only four discrete technologies, the number of tests per campaign had gradually increased each year. Around 53 technologies were tested on the Boeing 777-200 used in the 2019 event, and together with previous ecoDemonstrator programs, the upcoming campaign will bring the total number of new features tested over the life of the effort to almost 200.
“We have introduced about a third of those technologies onto our products and services,” Lutters says. “Of the remaining quantity, about half of those technologies continue onward in development, and the other half we decided that we’ve learned enough, and we have chosen not to invest further,” she adds. Technologies validated through the program that have been introduced onto Boeing products include the split winglet on the 737 MAX, touch-screen displays on the 777X and the use of SAF.
“This year we’re pushing the limits on the production system for SAF and trying to get to that certified 50:50 blend as much as possible,” Lutters says. “It has provided some great learnings in terms of where it is available.” The SAF is being supplied by World Energy Paramount in California. “[The] vast majority of the fuel used on the 2021 ecoDemonstrator is a 50% SAF blend with conventional Jet A,” Boeing says.
Early this year, Boeing announced that it intends to certify all its products to use 100% SAF by 2030.
The 737-9 has also been used for ground tests of a new fire-extinguishing agent for aircraft that is intended to replace Halon 1301, which is no longer being produced. The aerospace industry has been working to find effective replacements for ozone-depleting Halon in aircraft fire-extinguishing and suppression systems in the cabin, lavatories, cargo hold, engines and auxiliary power units since production of the chemical was banned in 1994.

Although non-Halon solutions have been found for cabins and lavatories, the industry is still forced to recycle Halon until effective replacements can be developed for the unique challenges of fire suppression at altitude in engines, auxiliary power units and the cargo hold. The 2019 ecoDemonstrator tested a new blend of bromotrifluoropropene (BTP) developed by Boeing and fire-suppression specialist Meggitt that showed promise for use in cargo holds. The “Blend D” agent, which has already passed the FAA minimum fire-suppression performance standards for Halon 1301, mixes BTP with an inert gas such as nitrogen or CO2 and was assessed for dispersion and concentration characteristics in flight.
The 737-9 is specifically testing a Meggitt-developed agent dubbed CF3i (iodotrifluoromethane) for extinguishing engine bay fires. “We think it’s now about ready to be certified,” says Doug Christensen, chief architect for the ecoDemonstrator. CF3i, which is used for fire extinguishing in the oil and chemical industry, is also tapped as a Halon replacement in some military aircraft. It breaks down before it reaches the stratosphere and so has low global warming potential.
Building on previous tests conducted with the FAA, Boeing’s work has focused on using CF3i to suppress fire involving different kinds of jet fuel, hydraulic fluid and engine oil, as well as varying spray patterns and volumes. For the final push toward certification, the ecoDemonstrator was used to evaluate the flow during ground runs with the left Leap 1B engine at high power to generate greater mass flow through the nacelle. These tests simulated some of the hardest conditions for meeting extinguisher-agent concentration requirements and helped engineers revise the positioning of delivery nozzles to achieve FAA standards.
The program has also tested acoustic lining concepts in the aft fan duct of one of the aircraft’s CFM Leap 1B engines, to evaluate potential noise reductions on current engines as well as inform designs for next-generation models. Conducted in conjunction with the FAA’s Continuous Lower Energy, Emissions and Noise (Cleen) program, the tests focused on treated thrust reverser blocker doors as well as specially developed acoustic gloves between the centerbody of the aft fan bifurcation duct and the inner walls of the thrust reverser.

Boeing says flight tests validated the design concept and pave the way for savings of up to 0.6 EPNdB on retrofit packages for current engines, as well as noise reductions of up to 1.2 EPNdB or more for ultra-high-bypass engines on future aircraft starting in 2025.
The 737-9 test work also includes collaboration with the U.S. National Oceanic and Atmospheric Administration to measure greenhouse-gas levels in the atmosphere to support the agency’s climate modeling and long-term forecasting. The testing is focused more on the design and integration of the sensors into commercial aircraft rather than the sensor type itself, and it includes an internal sensor mounted in an environmental control system duct in the wing root as well as a fuselage-mounted external probe.
As part of the drive to reduce life-cycle environmental impact, the cabin interior is partially configured with sidewall panels made from recycled carbon-composite material salvaged from the 777X wing production site in Everett, Washington. Testing has focused on the acoustic properties of the panels, which are considered rare examples of recycling for high-value aerospace components. Previous ecoDemonstrators have tested both advanced “acoustically tuned” sidewall designs to minimize vibration as well as other cabin features made from recycled materials. These have included a carpet tile evaluated in 2012 and, in 2019, an improved 100% recyclable version developed by flooring specialists InterfaceFLOR for commercial use.
The ecoDemonstrator is also being used for tests of a portable box emitting ultraviolet (UV) light from the cabin ceiling to sanitize the interior. “We are really focused on continuation of the confident travel initiative,” says Lutter, adding that the tests build on earlier technology—including a Boeing-developed UV wand that was validated on the 2020 ecoDemonstrator. The wand is now manufactured by Florida-based lighting specialists Healthe and is used to disinfect flight decks in under 15 min. The device uses 222-nanometer light in the UV-wavelength to kill pathogens without harming human skin tissue.
“We are looking to see how far UV can be utilized in the cabin, as compared to when we used it in a lavatory in the 2019 ecoDemonstrator,” she adds. Other technologies being tested include a 3D-printed passenger air vent design that is intended to produce an air curtain to mitigate the spread of airborne particles through the cabin.
The aircraft is being used to test a low-profile LED anti-collision beacon, too. This is typical of a technology that, without the existence of the ecoDemonstrator, would not by itself justify evaluation in a flying testbed. The light, which is a lower-drag evolution of the LED beacons used on the 787, is attached to a window plug midway along the port fuselage. “We wanted to have instrumentation connected up to this light to make sure we know it’s on and operating the way we expect it to,” says Lutters.
“We want to see how it operates in the airstream really, and it would be great if we could see how it does in ice and snow,” she adds. “And, although obviously we’re flying mostly during the summertime so we’re not getting all of that data, we are going to have it there for about five months of flying. So far it’s been holding up really well.”
The ecoDemonstrator is also being used to evaluate enhanced air traffic management connectivity with Inmarsat’s Iris data link satcom system. The current tests follow trials of a baseline internet protocol suite communications management unit on the 2019 ecoDemonstrator, a 777-200, and together represent the first trial of end-to-end cockpit-to-ground internet protocol satellite communications for more efficient operations (AW&ST Sept. 27-Oct. 10, p. 50).
Touch-screen cockpit display units (CDU) are also being tested in the ecoDemonstrator, building on earlier trials in 2014 that led to introduction of the technology on the 777X. The screens are lighter than the conventional push-button units, and human-factors experts are monitoring how flight crews interface with the CDUs to validate ease of use and potential efficiency improvements. If all goes well, the touch-screen CDUs could also enable some other cockpit radio panels to be removed, and the system could form the basis of a future flight deck upgrade for the 737 MAX.