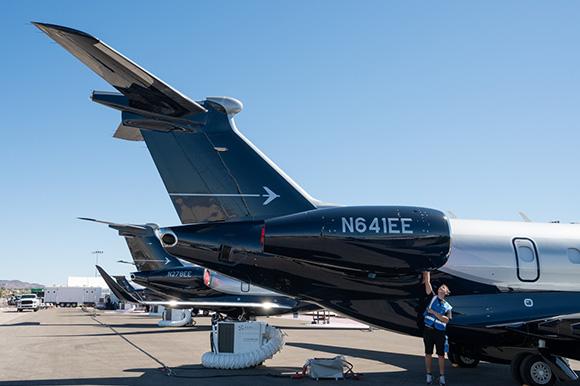
LAS VEGAS—With around 300 new HTF7000-family engines being produced every year and the super-midsize fleet building quickly with new orders, Honeywell Aerospace is ramping up its advanced prognostics capabilities to maintain higher levels of dispatch reliability.
In service on the Bombardier Challenger 300/350, Gulfstream G280, Embraer Legacy 500/450 and the Cessna Citation Longitude, the 6,500-7,600 -lb.-thrust HTF7000 series is “really a workhorse in the segment,” says Carl Kotlarz, senior product director, HTF7000, Honeywell Aerospace.
Maintaining reliability is “a pain point that we want to make sure that we are addressing, and we continue to improve upon,” says Kotlarz. “We're in unprecedented territory in terms of dispatch, reliability right now and we've done that with targeted improvements, our data and our advanced prognostics.”
The company is “leaning forward on things like our carbon seals bimodality, oil pumps, power shaft bearings and low-pressure turbine hard coat blades,” says Kotlarz. “Our theory is not to go to failure but go to ‘at access,'” he adds referring to replacement of a component as required ahead of scheduled maintenance.
“These are the things that we felt were the ones that we had to tackle first,” says Kotlarz. “We're looking at some of the additional items and maybe perhaps some line replaceable units (LRU) and additional improvements going forward to ensure that we continue to drive that dispatch reliability. Some of those we have to unlock with more frequent data,” he adds.
Using the company’s Connected Services system—a combination of big data, analytics and secure communications technology—Kotlarz says experience has shown that issues can be anticipated ahead of developing into aircraft-on-ground (AOG) problems. “We detected a condition where the No. 4 carbon seal wears and produces a bimodal signature in the data for oil pressure. We can detect the variation of that and predict very accurately how close it is to a failure.”
In this case operators are given a 90-day window during which they can continue to operate but must also ultimately replace the seal. “We don't let the engine tell them when it needs maintenance. They get to choose,” says Kotlarz, who adds that the “two programs we ran around bimodality and our compressor abradable seal really validated for the operator community the power of the data.”
Previously, says Kotlarz, “maybe operators viewed it as just data that Honeywell used to control costs. Now they're seeing that it actually can be turned around and used to improve their uptime, which is really what we're trying to accomplish. And there's more to unlock. We believe that the more frequently we get the data and the more data we can get, the more we can continue to develop signatures of certain conditions and help the aircraft achieve its uptime.”
Honeywell is meanwhile conducting a detailed borescope inspection of an HTF7500E that was used in a recent demonstration flight of an Embraer Praetor 600 with 100% sustainable aviation fuel (SAF). The tests, with the left engine running on 100% SAF, were performed at Embraer’s Melbourne, Florida, facility with SAF provided by World Fuel. “The left-wing fuel tank was 100% SAF for the roughly 1 hr. flight test, during which it flew 350 nm. Now we have some work going into borescoping and collecting data but the engine performed flawlessly,” says Kotlarz.